21 July 2025
Understanding product recalls in the GLOBALG.A.P. system
What is the recall and withdrawal principle, and how does the GLOBALG.A.P. certification system support identification and traceability mechanisms in the supply chain?
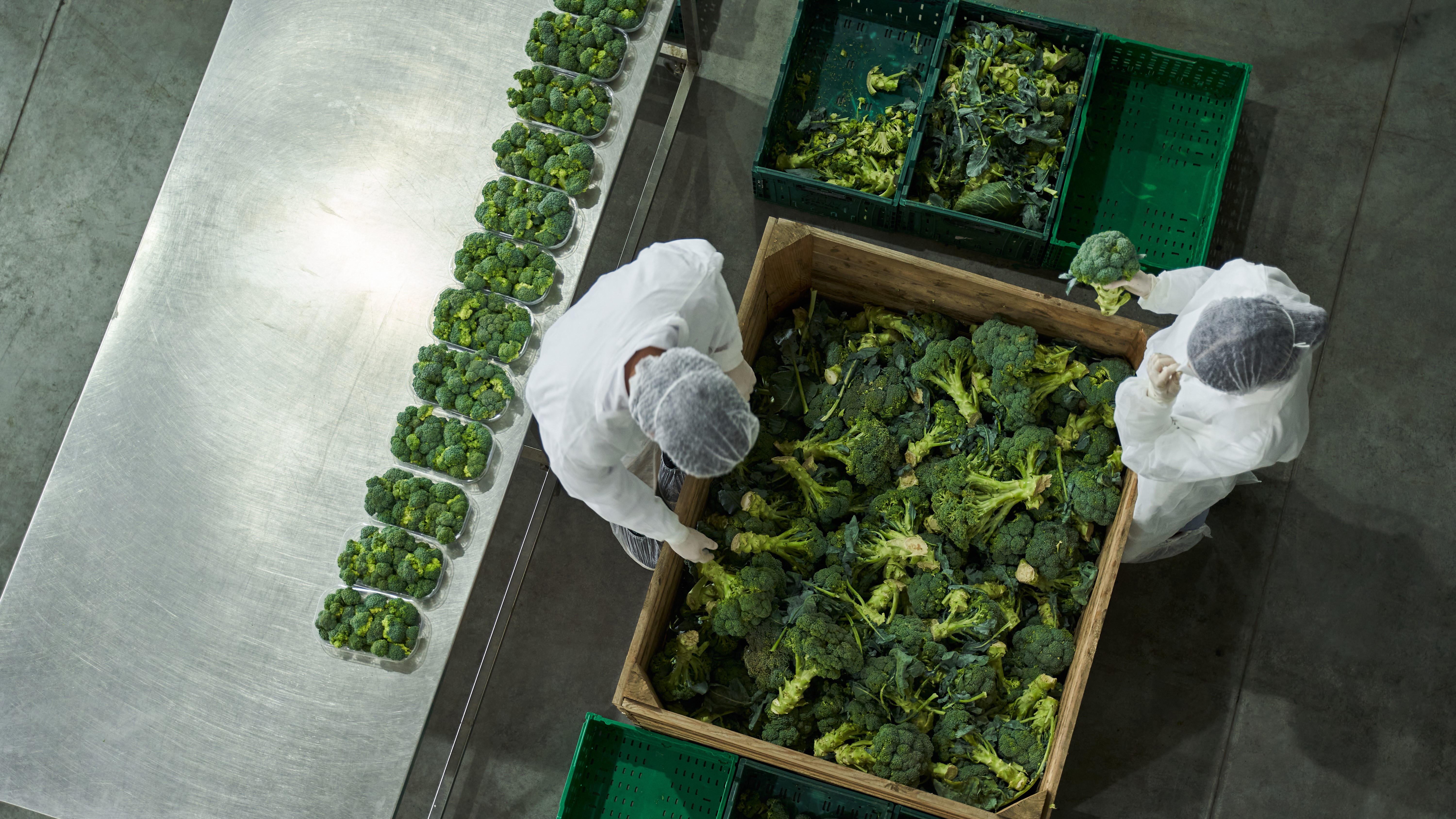
A product recall is a process initiated by a supply chain stakeholder (e.g. producer, packer, trader, retailer) or a regulatory authority to identify and remove a product from the market due to safety concerns or non-compliance with regulations.
Identifying the affected product, informing buyers and consumers, and providing instructions for the safe handling, return, or disposal of the product are essential steps in a successful recall.
Recalls can be initiated for a wide variety of reasons and managing the process quickly and transparently is of vital importance, regardless of the origin of the recall issue.
As a core pillar of the GLOBALG.A.P. standards for over 20 years, food safety is a major component of our solutions. While standard criteria on the recall and withdrawal principle address the identification, communication, and traceability mechanisms involved in the process, there are several factors which can impact its effectiveness in practice.
Communication
The quick dissemination of information to supply chain stakeholders is essential. This may involve several channels to ensure visibility and support correct action. Communication efforts may involve ongoing updates on efforts and resolutions, as well as support for buyers or consumers with concerns.
A delayed response to a product recall issue has the potential to not only damage trust with buyers and consumers, but also increase risks and inhibit the proper steps to resolving the issue in the supply chain.
Accuracy
Messaging during a recall process must be clear and detail-oriented, explaining both the reasons for the withdrawal and the next steps to be taken. Specific information on affected products, how they can be identified, and how they should be handled must be provided to mitigate further risks.
Insufficient detail can increase the time it takes to react to the product recall, potentially causing panic in supply chains if impacted products cannot be clearly and transparently identified.
Traceability
The supply chain stakeholder responsible for the recall must share information on batch/lot numbers, as well as where and to whom the product was sold. This process may involve multiple companies and locations, depending on the product.
Low awareness – for example, if recall information is difficult to find or obtain – may result in a lack of coordinated action in complex supply chains.
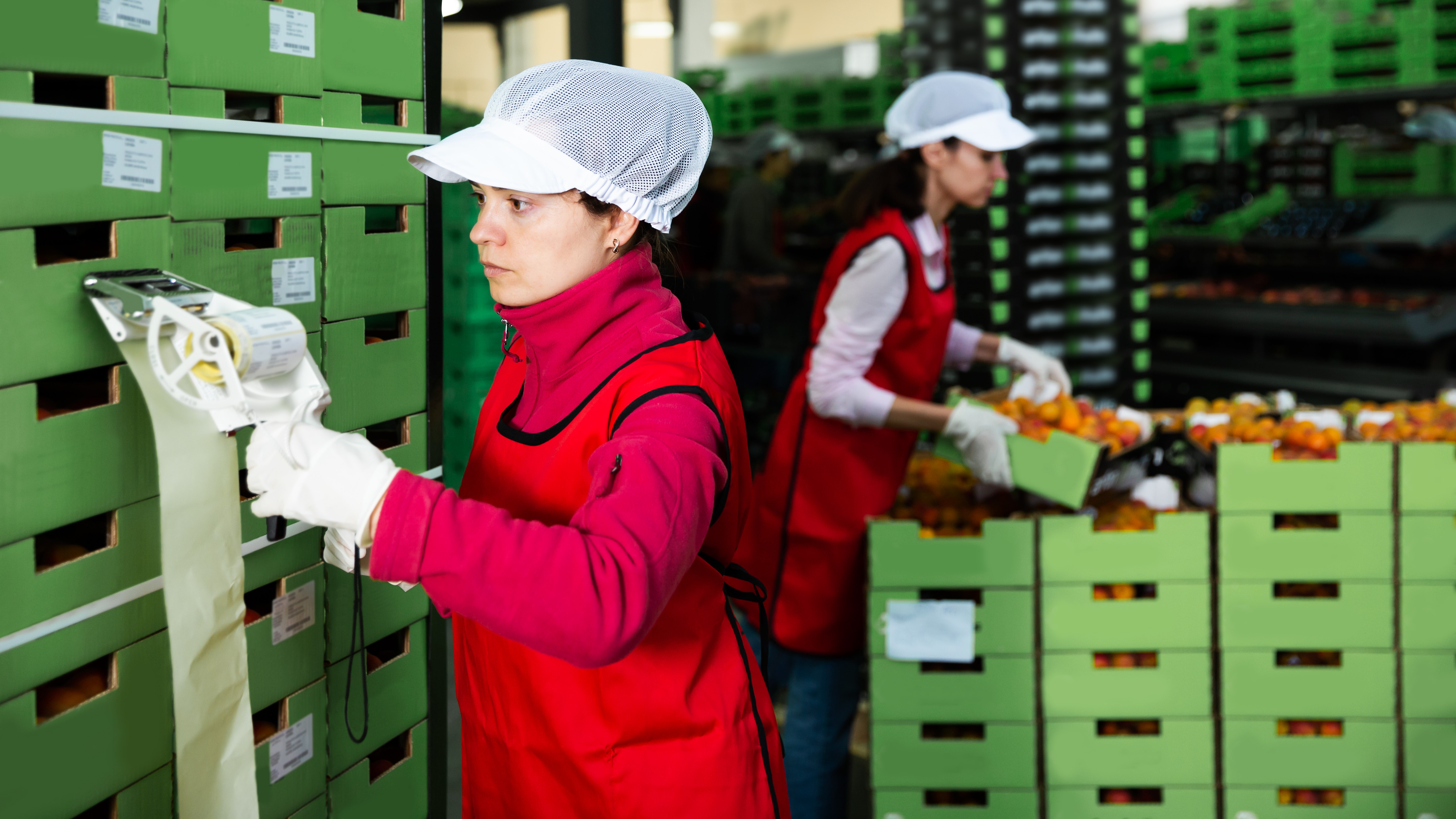
Recall and withdrawal in GLOBALG.A.P. standards
All standards in the GLOBALG.A.P. core solutions category feature principles and criteria (P&Cs) addressing the process of product recall and/or withdrawal. The relevant criterion is graded at Major Must level, requiring 100% compliance from the producers, manufacturers, and supply chain companies who implement our standards. Requirements cover documented procedures to manage the recall and withdrawal of products from the marketplace. Such procedures must identify:
The types of events that may result in a recall and withdrawal
The persons responsible for making decisions on the recall and withdrawal
The mechanism for notifying the next step in the supply chain
The notification of relevant authorities
Steps taken to contact the certification body (CB), which in turn may contact Agraya GmbH
The methods for reconciling stock
Crucially, the recall and withdrawal procedure must be tested annually for effectiveness, with the results of the mock recall recorded during the CB audit.
Moreover, to maintain the integrity of the GLOBALG.A.P. system, a certified company must immediately report to Agraya GmbH any event that might have a negative impact on their registration/certification status, or the GLOBALG.A.P. certification system as a whole, including, but not limited to, food safety outbreaks and recalls. The same rule applies in case a certified producer is informed by a competent and/or local authority that they are under investigation and/or have received a sanction within the scope of the certification due to a recall.
In such cases, a follow-up investigation shall be initiated by Agraya GmbH in cooperation with the responsible CB of the company involved in the recall, through an unannounced on-site assessment, to verify the compliance of the company with the corresponding principles and criteria of the applicable GLOBALG.A.P. standard.
Depending on the outcome of such an investigation, the certification of the company involved will be maintained in case of full compliance, or the company will be given time to make corrections to close any detected non-conformances against the applicable standard’s requirements. In serious cases of non-compliance with the applicable standard, a temporary suspension of the producer's certification may be imposed.
In cases where fraud and/or lack of trust in the company’s compliance with the applicable standard’s requirements is evidenced – or where a suspended company cannot show evidence of implementation of effective corrective actions before the suspension period set by the CB has elapsed – certification will be withdrawn and a cancellation will be imposed for 12 months, disqualifying the company from any type of GLOBALG.A.P. certification for that period.
These requirements support producers with GLOBALG.A.P. certification and supply chain companies trading products from GLOBALG.A.P. certified production processes in not only understanding the necessary steps in a recall procedure, but in effectively implementing them if an issue arises.
Traceability and non-conforming products
Recall and withdrawal procedures are complemented by further criteria on a traceability system and on requirements for non-conforming products, also graded at Major Must level. These aim to identify and segregate any products affected by food safety or quality issues before they enter the supply chain and potentially require the implementation of the recall and withdrawal procedure.
The traceability system enables registered products to be traced back to the registered farm or supplier, or to the registered farms or suppliers of a producer group and traced forward to the immediate customer (“one step forward and one step back”). Harvest information links a batch or lot to the production records or the farms of specific producers.
Products considered non-conforming – for example, due to a food safety issue, maximum residue limit exceedance, cross-contamination issue, etc. – undergo both segregation processes and root cause analyses. This enables the determination and implementation of corrective actions to prevent a recurrence of similar incidents in production.
Related links:
Learn more about the GLOBALG.A.P. impact areas, such as food safety
Explore GLOBALG.A.P. solutions for primary production
Discover how GLOBALG.A.P. supports responsible supply chains