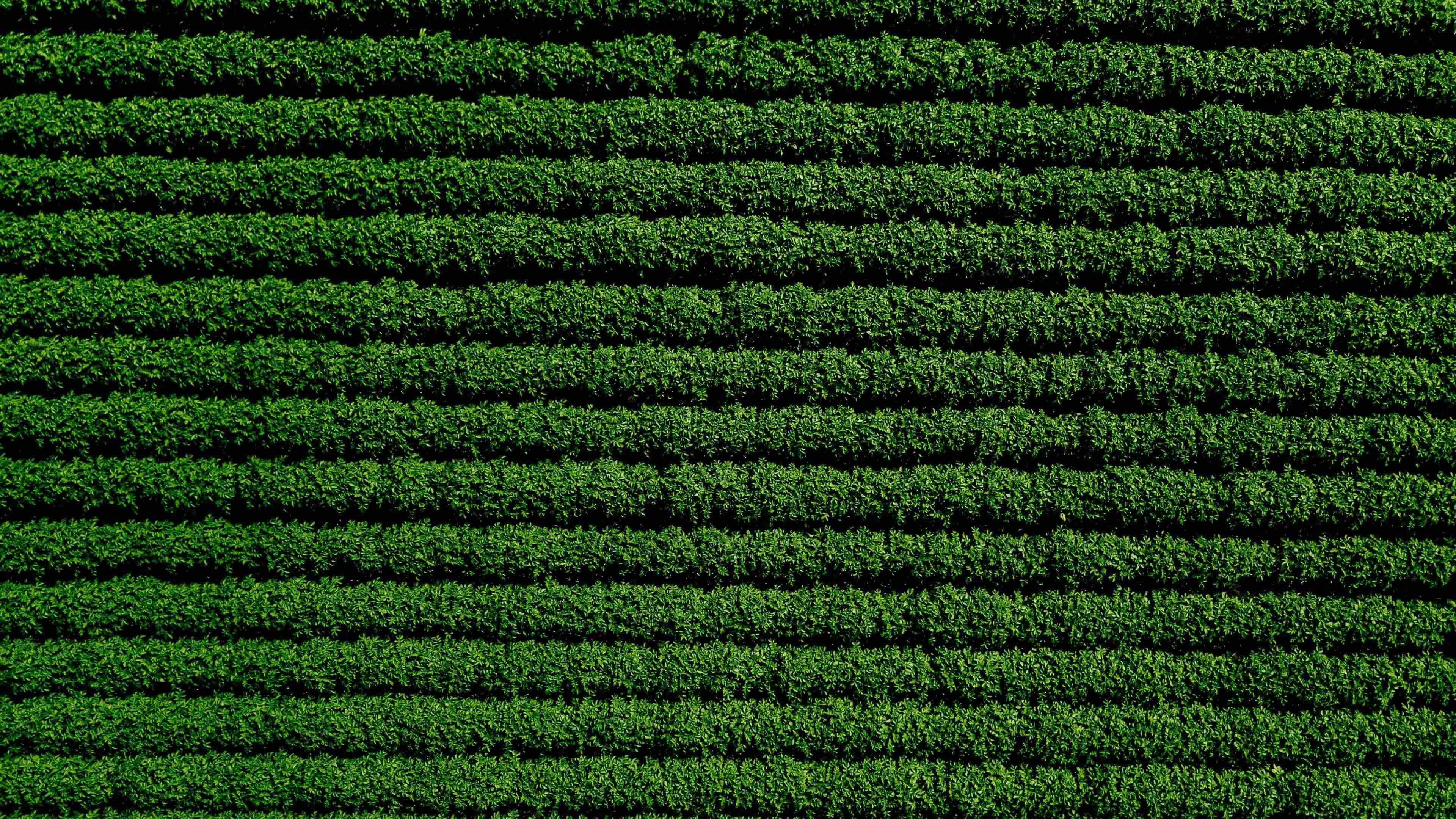
Technical news library
Technical news – Integrated Farm Assurance (IFA) entries
On this page you can find key entries and excerpts from the GLOBALG.A.P. technical newsletter that relate to the IFA standard. The complete and original technical newsletters are available in the GLOBALG.A.P. document center and the CB Extranet.
Sections in this page
Looking for technical news related to Chain of Custody, GRASP, and others?
All technical news related to our add-ons such as GRASP and SPRING can be found under technical news for add-ons.
Technical news related to other standards such as Chain of Custody, Produce Handling Assurance, or Compound Feed Manufacturing can be found under technical news for core solutions.
General IFA: Technical news (applicable for all product categories)
In “GLOBALG.A.P. general regulations – Rules for certification bodies,” sections 12.3.3 a) and 13.3.3 a), there is reference to the use of a translator: “This shall include the locally used specialist terminology in the respective working language or the use of a translator.”
Here the reference is to competent translators, not auditors.
Any other case, e.g., the use of local auditors (not necessarily approved for the audited standard/add-on) to facilitate the communication during the audit shall be handled as an exception according to “GLOBALG.A.P. general regulations – Rules for certification bodies,” sections 12.3.3 b) and 13.3.3 b), and CBs shall contact the GLOBALG.A.P. Secretariat before the audit.
As communicated in TN 3/2024, a producer group is a “group of three or more producers (see definition of producer) that apply for GLOBALG.A.P. certification organized under a QMS, according to GLOBALG.A.P. QMS requirements. The legal entity managing the QMS is the only certificate holder in this certification option. The approved producer group members are listed in an annex to the GLOBALG.A.P. certificate.”
We would like to clarify here that this definition applies for all GLOBALG.A.P. solutions, meaning the add-ons as well.
As described in “GLOBALG.A.P. general regulations – Rules for producer groups and multisite producers with QMS,” section 9.1, 7.2.e):
“The CB may additionally issue GLOBALG.A.P. certificates to producer group members if those members were audited as part of the sample. Such certificates shall be clearly distinguishable from certificates that are issued to individually certified producers (Option 1) and shall state explicitly that the recipient is part of a certified producer group. Any limitations to the scope of certification shall be transparent to customers.”
We would like to remind CBs that the above-mentioned documents must be developed by the CBs and are not generated by the GLOBALG.A.P. IT platform.
If a CB needs to register a new branch that shall appear on the GLOBALG.A.P. website, please provide the following information about the branch to cb_admin@globalgap.org:
Name of the branch
Full address
Main contact
Phone number
Website (optional)
As described in “GLOBALG.A.P. general regulations – Rules for certification bodies,” section 7, “Audit process,” the CB audit content shall be organized in a three-year cycle. For the audits in years 2 and 3, checklists will be available for CBs in the GLOBALG.A.P. IT platform.
In TN 2/2024 we announced that CBs have access to the list of operational and non-operational items (not the CB audit checklists for years 2 and 3) in the audit method and justification guidelines for the Integrated Farm Assurance (IFA) standard version 6 Smart and GFS for fruit and vegetables and IFA v6 Smart for flowers and ornamentals, as well as for IFA v6 Smart and IFA v6 GFS for aquaculture. This list was also made available in the CB Extranet for IFA v6 Smart and IFA v6 GFS for quality management systems (QMS) and IFA v6 Smart for hops.
Due to the transition to our new GLOBALG.A.P. IT platform, we announce that the CB audit content organization in a three-year cycle is, until further notice, currently optional and not mandatory. CBs may choose to consider the guidance for the non-operational items when planning audits in years 2 and 3, or they may audit all principles and criteria (P&Cs) as operational.
In all cases, CBs shall still audit every P&C, and the overall minimum audit duration cannot be reduced.
Our attention was recently brought to GLOBALG.A.P. certifications in Western Sahara. We would like to share the results of our evaluation related to identifying the origin of products grown in the area.
According to Article 73 of the United Nations Charter, Western Sahara remains classified as a “non-self-governing territory,” and recent European Court of Justice (ECJ) rulings have confirmed that trade agreements between the European Union and Morocco do not extend to Western Sahara without the explicit consent of the Sahrawi people.
The ECJ has also ruled that products originating from Western Sahara must be explicitly labeled as such and must not be presented as Moroccan products.
On 15 July 2024, the International Accreditation Forum (IAF) signed a Scheme Endorsement Agreement with GLOBALG.A.P. c/o FoodPLUS GmbH in recognition of the IFA standard version 6.
The IAF is a leading association of accreditation bodies, conformity assessment bodies, and other organizations working to develop a single international program for conformity assessment. In 2013, IFA was the first scheme to receive IAF endorsement under the Multilateral Recognition Arrangement (MLA) scope of Product Certification.
The latest version of the flagship GLOBALG.A.P. standard – launched in late 2022 – replaced IFA v5.2 on 1 January 2024 for the product categories of fruit and vegetables, flowers and ornamentals, hops, and aquaculture. Please note that the PHA standard has also been endorsed by the IAF.
Mutual recognition of accredited certification
The MLA marks an agreement for the mutual recognition of accredited certification between IAF Accreditation Body Member signatories.
These signatories are then required to recognize certificates and verification statements issued by CBs accredited by all other signatories of the MLA with the appropriate scope.
About MLA levels
The IAF MLA consists of five levels. Level 4 sub-scopes are IAF-endorsed normative documents used by accreditation bodies in conjunction with main scope documents to assess a CB’s competence in a specific sector. Level 5 sub-scopes are IAF-endorsed normative documents used by CBs.
The new scheme endorsement agreement includes the GLOBALG.A.P. general regulations v6 under level 4 and the IFA v6 Smart/GFS principles and criteria (P&Cs) under level 5.
Previously communicated in TN 02/2024
Due to the war in Israel and the Palestinian territories, the GLOBALG.A.P. Secretariat has offered the possibility to activate the emergency procedure for certificate validity extension for a maximum period of six months. Here we would like to remind you that this exception also applies to Ukraine.
In addition, certification bodies that are not able to conduct on-site inspections/audits due to the current official travel restrictions and state of emergency circumstances (“force majeure”) in Israel (including Israel and the Golan Heights; Israel and the West Bank), Lebanon, the Palestinian territories, and Ukraine are allowed to conduct inspections/audits remotely following the GLOBALG.A.P. Remote procedure (version 1.3)/GLOBALG.A.P. Full Remote procedure version 6 (for IFA v6 Smart audits).
The time frame for the application of the GLOBALG.A.P. Remote procedure is:
Until further notification
As soon as the situation in these areas improves, we will communicate the timeframe by when this exception will be phased out.
The GLOBALG.A.P. Secretariat will continue to communicate updates on this topic and remains available to respond to questions or concerns.
We would like to inform you about the IFA v6 national interpretation guidelines (NIGs) that are already published and available on our website.
In the countries listed below, CBs shall use the new NIGs for IFA v6. The relevant countries are:
For IFA v6 Smart/GFS for aquaculture: Colombia
For IFA v6 Smart for fruit and vegetables: Albania, Belgium, Ecuador, Japan, Italy, Albania, France, Spain, India, the Netherlands
For IFA v6 Smart for flowers and ornamentals: DACH countries (one common NIG for Germany, Austria, and Switzerland)
Previously communicated on 23 September 2024
We would like to call your attention to the implementation of the residue monitoring system (RMS) checklist version 6:
1. Introduction
The RMS approach was introduced in IFA v4, as an alternative for the 100% testing by product, site, and production cycle.
The RMS is based on a risk assessment by product, and the outcome of the risk assessment is a monitoring program by product. The monitoring program defines the number of samples by product for a group of producers. This can be a group of Option 1 individual producers participating in the RMS of an independent RMS operator; or it can be the members of an Option 2 producer group participating in the RMS of the group.
For IFA v6/RMS v6, the GLOBALG.A.P. Secretariat has added two new elements:
A minimum number of samples must be taken for each product, based on the number of participating sites.
A performance-based approach, in which the number of maximum residue limit (MRL) exceedances is leading for the applied sampling table: reduced, standard, tightened, or 100%.
Both new elements are based on the ISO 2859 standard for attribute testing. The justification of the GLOBALG.A.P. Secretariat for adding these two new elements is to increase the credibility of the IFA standard based on an internally accepted standard.
2. Registration in the GLOBALG.A.P. database
2.1 Registering an RMS operator
An independent RMS operator offering RMS services to Option 1 individual producers shall be registered in the GLOBALG.A.P. database as a producer. (There is no alternative name available in the database.) As a result of the registration, a GLOBALG.A.P. Number (GGN) is generated.
Option 2 producer groups operating their own RMS for their members do not need further registration. The GGN of the producer group is used.
2.2 Registering an RMS
Registration of the RMS in the GLOBALG.A.P. database is mandatory for independent RMS operators but voluntary for Option 2 producer groups.
Go to “Manage products” in the database.
Select the scheme RMS checklist version 6.
Select product RMS 1. Note: An RMS operator might have more than one RMS. A maximum of 10 RMSs can be registered under the same GGN (RMS 1 to RMS 9). If only one RMS is operated, please select RMS 1.
Register the number of products in the scope of the RMS and the number of producers participating in the RMS.
Select the applicable value for the attributes: product category, scope of activity, and type of sampling.
2.3 Acceptance and certification of an RMS
These steps follow the same procedure as for any other product and can be accessed in the database through “Acceptance” and “Certification”.
2.4 Uploading the RMS checklist
The RMS checklist shall be shared with the GLOBALG.A.P. Secretariat and uploaded to the GLOBALG.A.P. database.
The RMS checklist for an Option 2 producer group is integrated in the IFA QMS checklist. No separate upload of the RMS checklist is needed.
3. Miscellaneous
If the first buyer is a company with GLOBALG.A.P. Chain of Custody (CoC) certification, the RMS operator is allowed to sample the products of producers at the facilities of the company with CoC certification. The first buyer may operate its own RMS.
If the participating producers of an RMS are certified to IFA 5.4-1-GFS, the previous RMS checklist version 5.2 is still valid. If one or more of the participating producers is certified to IFA v6 Smart or IFA v6 GFS, the RMS checklist version 6 applies.
In the GLOBALG.A.P. CB Academy, a self-paced training is available to make yourself familiar with the rules of RMS checklists and the sampling tables.
The GLOBALG.A.P. RMS Platform will be launched in Q4 of 2024 (postponed to 2025). This platform offers RMS operators and individual producers the option to share MRL test results with GLOBALG.A.P. participants and their products will be visible on the GLOBALG.A.P. website. Participants will also receive a monthly aggregated report on MRL test results. More details about the GLOBALG.A.P. RMS Platform will be shared in an upcoming briefing.
4. Summary
Producers can still do self-sampling for residue testing, and producer group members can still test all their registered products, following a risk assessment.
Option 2 producer groups and Option 1 multisite producers with QMS may develop their own RMS for their members/production sites. That will be audited during the CB QMS audit.
Option 1 individual producers may participate in the services of an independent RMS operator if this RMS is audited by CBs.
The CB-audited RMS (independent RMS operator, or RMS operated by an Option 2 producer group) may become visible in GLOBALG.A.P. RMS Platform after the operators’ application to rms@globalgap.org and approval by the GLOBALG.A.P. Secretariat.
The launch of the GLOBALG.A.P. RMS Platform has been postponed to early 2025. The GLOBALG.A.P. RMS Platform validates GGNs and certification statuses in the GLOBALG.A.P. database. The GLOBALG.A.P. database will be replaced in Q4 of 2024 by the osapiens supply chain portal. Once the osapiens portal is operational, the GLOBALG.A.P. RMS Platform will be connected to this portal.
Note: The GLOBALG.A.P. RMS Platform is available for testing on the present GLOBALG.A.P. test database until the end of 2024. Applications to participate in the GLOBALG.A.P. RMS Platform can be sent to rms@globalgap.org. You can find more information on the GLOBALG.A.P. website, or write to standard_support@globalgap.org if you have any questions.
As described in the GLOBALG.A.P. general regulations, “a documented or electronic confirmation by the producer is accepted as equivalent to the producer’s signature.”
Similarly to this and from now on, the witness audit report shall contain handwritten or genuine and valid digital signatures of both auditors: the witnessed auditor and the auditor performing the witness audit. JPG images are not considered valid signatures.
We would like to remind you of the communication sent out in TN 02/2022, section 2.1: The assignment to the IFA v6 GFS plants/aquaculture scope shall be done by the CBs and shall only be done for CB auditors that have already been signed-off and approved for IFA v5.4-1-GFS. These CB auditors shall complete the necessary GLOBALG.A.P. online training (e.g., for CB QMS auditors) and pass the auditor online tests for the relevant scope within one month after release in their working language. New CB auditors shall follow the initial sign-off and qualification process for IFA v6 GFS.
CB auditors previously approved for IFA v5.2 or currently approved for IFA v6 Smart are considered “new” auditors for IFA v6 GFS, and the initial sign-off process described in the “GLOBALG.A.P. general regulations – Rules for certification bodies,” sections 12, 13, and 14.1 shall apply.
According to the “GLOBALG.A.P. general regulations – Rules for certification bodies,” sections 12.3.5.d) and 13.3.5.e), “the CB shall carry out a CB farm witness audit/CB QMS witness audit for each of its GLOBALG.A.P. CB farm auditors/CB QMS auditors at least once every four years to verify competence.”
We would like to clarify here that these witness audits shall be done by competent CB farm auditors, witnessing CB farm auditors, or CB QMS auditors, witnessing other CB QMS auditors.
Witness audits conducted by accreditation body assessors cannot count toward compliance with this competency requirement.
After the last GFSI office assessment we decided to update the definition of producer groups as described in IFA v6 glossary. The definition is adapted for both IFA v6 Smart and IFA v6 GFS to:
“Group of three or more producers (see definition of producer) that apply for GLOBALG.A.P. certification organized under a quality management system (QMS), according to GLOBALG.A.P. QMS requirements. The legal entity managing the QMS is the only certificate holder in this certification option. The approved producer group members are listed in an annex to the GLOBALG.A.P. certificate.”
And the definition of group certification is now adapted to: “The option to apply for GLOBALG.A.P. certification as a group of producers (three or more) where a quality management system (QMS) is implemented. The group, as a legal entity, is the certificate holder once certified.” This producer group might consist of three members or the group itself with its own production sites and two more producer group members.
The producer group may “lose” some producer group members during the certificate validity without applying a suspension. However, during the CB surveillance audit, the producer group shall have at minimum three producer group members. Otherwise, a certificate suspension shall apply.
Also, during re-registration and before the next recertification audit, the producer group shall have at minimum three members. If not, the CB shall not accept this re-registration as an Option 2 producer group.
These new definitions shall apply for any new certification or recertification audit to IFA v6 Smart or IFA v6 GFS, after the publication of this Technical News issue.
We would like to inform CBs that the GLOBALG.A.P. Secretariat has developed guidelines to support CBs facing logistical challenges when implementing unannounced audit procedures.
The purpose of this document is to present key points for consideration that may help CBs create operational procedures to facilitate the unannounced CB audit process while minimizing the risk of unannounced CB audits being rejected and producers subsequently being sanctioned.
The document “Implementing effective unannounced audit procedures – Guidelines for certification bodies” is available for CBs in the CB Extranet and is a guideline, not an obligatory or normative document.
After the last Integrity Surveillance Committee (ISC) meeting, it was decided to amend the following sections of the “GLOBALG.A.P. general regulations – Rules for certification bodies”:
a) Section 10.1 c) (iii): Increase of the daily ISC cost reimbursement fee from €1,000 to €1,200 per day.
During the 36th ISC meeting, the decision was made to increase CBs’ cost contribution to €1,200 per man-day of CIPRO assessment. The decision was made due to the increase in logistical costs of CIPRO reassessments in recent years. The cost contribution had not been changed in the past ten years. The new cost contribution will be applicable from October 2024 (the 37th ISC meeting) and will be re-evaluated in 3 years’ time.
However, the GLOBALG.A.P. Secretariat will only implement this cost reimbursement fee obligation and send out the invoices after the notification of the final decision of the ISC (due to the outstanding decision of the reassessment fees for CBs).
b) Clarification of section 11.3: The definition of the Second Warning in section 11.3.2 of the “GLOBALG.A.P. general regulations – Rules for certification bodies” indicates that the Second Warning occurs after the First Warning if the First Warning is not closed. However, the GLOBALG.A.P. general regulations also state that warnings are not consecutive. Therefore, a CB may receive a Second Warning directly, without having received a First Warning beforehand.
As communicated in TN 03/2023 (content adapted since TN 03/2023): We would like to inform you that sections 12.3.5 i) and 13.3.5 i), found under section 14, “Additional requirements for IFA v6 GFS,” in the “GLOBALG.A.P. general regulations – Rules for certification bodies,” are to be replaced by the following text:
“The CB shall have in place a procedure to ensure that annually every auditor conducts at least five on-site audits at a number of different producers.
In the case of a CB auditor approved for GFSI-recognized GLOBALG.A.P. standards, the audits required for maintenance of competency shall be against any GLOBALG.A.P. GFSI-benchmarked GLOBALG.A.P. standards with at least one of these annual on-site audit being against the respective GFSI-recognized GLOBALG.A.P. standard.
If this requirement cannot be met, the CB auditors shall carry out 5 on-site audits against any GFSI-approved Certification Programme (see list here), with at least one of these annual on-site audits being against the respective GFSI-recognized GLOBALG.A.P. standard.
For example, a CB auditor may conduct 4 audits to any GFSI-approved Certification Programme and only one audit to IFA v6 GFS to maintain competency for IFA v6 GFS.”
As communicated in TN 03/2023 (content adapted since TN 03/2023): As it reads in the “GLOBALG.A.P. general regulations – Rules for producer groups and multisite producers with QMS,” section 6.1.2.1. e), under section 14, “Additional requirements for IFA v6 GFS,” “at least 25% of the sample shall be randomly selected from the actual number of producer group members/production sites.”
We would like to remind CBs to record in the GLOBALG.A.P. IT systems (Audit Online Hub (AOH)) the producer group members/production sites randomly selected.
Text is also added to section 6.1.2.1 e), under section 14, “Additional requirements for IFA v6 GFS” in the “GLOBALG.A.P. general regulations – Rules for producer groups and multisite producers with QMS” (changes underlined):
“Selection of members/sites shall be based on the risk assessment carried out by the CB. However, at least 25% of the sample shall be randomly selected from the actual number of members/sites.
The risk assessment shall include consideration of the members’/sites’ internal audit program findings and the sites’ specific risks.”
The changes above will be included in the next update of the IFA v6 normative documents (IFA v6.1) and will additionally apply to the Harmonized Produce Safety Standard (HPSS).
We would like to remind you that reasonable precautions shall be taken by producers, as described in the requirements of the GLOBALG.A.P. IFA standard, to effectively minimize the risk of contamination arising from the presence of birds on the farm, especially during harvest (farm level) and postharvest (storage and/or packing level) operations.
The IFA standard’s requirements focus on the protection of harvested products and harvest containers if they stay outdoors in the field, and on the efficient closing of produce handling facilities (indoor storage or packing), to avoid birds nesting inside through adequate control of entrance points (e.g., via window netting, use of strip curtains in entrances, etc.). Furthermore, there is no requirement in the IFA standard for a producer to kill birds or to destroy or remove their nests.
If a producer has developed means to effectively control the associated risks and can demonstrate this through adequate measures and justifications, the presence of birds (e.g., swallows) and their nests could be allowed near outdoor production areas, for example in on-farm corridors or small landscape structures that are used to improve connectivity for the species on landscape level and protect and promote local wildlife species that are established in the farm’s agricultural area (e.g., trees, groups of trees, hedges, and small ponds). If providing nesting for the birds outdoors, the producer shall place the nests in places that minimize the risk of product contamination.
In cases where a birds’ nest is already established within the production area, appropriate measures shall be planned and taken by the producer to reduce possible product contamination without using destructive techniques to rid the production area of the nests.
Compliance with GLOBALG.A.P. standards is also based on locally applicable legislation, where in some countries removing or destroying specially protected species’ already established nests in indoor packing/storage facilities is prohibited. Therefore, GLOBALG.A.P. standards do not require such techniques from producers.
Please consider and compile the cross-requirements from the following sections of the IFA v6 normative documents during your audits:
“GLOBALG.A.P. general regulations – Rules for individual producers,” section 1, “Introduction,” fifth paragraph: “Legislation relevant to principles and criteria (P&Cs) more demanding than GLOBALG.A.P. requirements overrides the GLOBALG.A.P. requirements.”
IFA v6 Smart P&Cs for fruit and vegetables:FV-Smart 19.07: “Appropriate measures shall be taken to reduce possible product contamination by animals within the production area. Where there is evidence of animal activity that may result in product contamination, appropriate measures shall be taken. Eliminating wildlife or using destructive techniques to rid the production area of all animals are not considered appropriate measures.”
FV-Smart 21.01: “The risk assessment shall be:
Available for all production sites, including structures
Reviewed at least annually or when changes occur (new risks emerge or new sites or crops enter production)
It shall consider: Biological, physical, and chemical hazards...”
FV-Smart 21.02: “A management plan shall:
Be reviewed together with the risk assessment (annually or when changes occur) and address all risks identified in the risk assessment
Describe the control measures implemented for the risks identified
Be appropriate to farm operations..."
FV-Smart 22.01.01: “A documented biodiversity plan for the farm shall be available. This can be a generic plan that has been made farm-specific. This biodiversity plan shall:
Take into account local legislation and tailor the plan contents to the on-farm reality (open field, greenhouse, vertical farming, etc.)”
Previously communicated in TN 01/2024
Due to the war in Israel and the Palestinian territories, and the dramatic earthquake that occurred in Japan early in January 2024 in the prefectures of Ishikawa, Fukui, Niigata, Toyama, and Nagano, the GLOBALG.A.P. Secretariat offered the possibility to activate the emergency procedure for certificate validity extension for a maximum period of six months.
In addition, certification bodies that are not able to conduct on-site inspections/audits due to the current official travel restrictions and state of emergency circumstances (“force majeure”) in Israel (including Israel and the Golan Heights; Israel and the West Bank), Lebanon, the Palestinian territories, and in Japan in the prefectures of Ishikawa, Fukui, Niigata, Toyama, and Nagano, are allowed to conduct inspections/audits remotely following the GLOBALG.A.P. Remote procedure (version 1.3)/GLOBALG.A.P. Full Remote procedure version 6 (for IFA v6 Smart audits).
The time frame for the application of the GLOBALG.A.P. Remote procedure is:
Up to 31 December 2024 for Israel, Lebanon, and the Palestinian territories
Up to 30 October 2024 for Japan’s prefectures of Ishikawa, Fukui, Niigata, Toyama, and Nagano
If further extension of the time frame of validity for applying the GLOBALG.A.P. Remote procedure is required, it will be communicated in a timely manner by the GLOBALG.A.P. Secretariat.
The GLOBALG.A.P. Secretariat will continue to communicate updates on this topic and remains available to respond to questions or concerns.
Previously communicated on 14 February 2024
Previously communicated on 12, 18, and 29 January 2024
Due to the war in Israel and the Palestinian territories, and the dramatic earthquake that occurred in Japan early in January 2024 in the prefectures of Ishikawa, Fukui, Niigata, Toyama, and Nagano, the GLOBALG.A.P. Secretariat offered the possibility to activate the emergency procedure for certificate validity extension for a maximum period of six months.
In addition, certification bodies that are not able to conduct on-site inspections/audits due to the current official travel restrictions and state of emergency circumstances (“force majeure”) in Israel (including Israel and the Golan Heights; Israel and the West Bank), Lebanon, the Palestinian territories, and in Japan in the prefectures of Ishikawa, Fukui, Niigata, Toyama, and Nagano, are allowed to conduct inspections/audits remotely following the GLOBALG.A.P. Remote procedure (version 1.3)/GLOBALG.A.P. Full Remote procedure version 6 (for IFA v6 Smart audits).
The time frame for the application of the GLOBALG.A.P. Remote procedure is:
Up to 30 June 2024 for Israel, Lebanon, and the Palestinian territories
Up to 30 July 2024 for Japan’s prefectures of Ishikawa, Fukui, Niigata, Toyama, and Nagano
If further extension of the time frame of validity for applying the GLOBALG.A.P. Remote procedure is required, it will be communicated in a timely manner by the GLOBALG.A.P. Secretariat.
The emergency procedure allowed for Ecuador was valid from 12 January 2024 to 15 February 2024.
The GLOBALG.A.P. Secretariat will continue to communicate updates on this topic and remains available to respond to questions or concerns.
Previously communicated on 11 January 2024
The GLOBALG.A.P. data access rules have been updated. Version 4.1 of the data access rules became mandatory on 1 February 2024 and is now available in GLOBALG.A.P. document center.
Changes made
Revisions in the data access group for CBs: visibility of company master data to certification bodies added (for search options)
New data access group for benchmarked certification system owners added and benchmarking added as a separate section (section 6)
New section added for historical data in VS
Removed: Produce Safety Standard (PSS) and product attribute “no use of antimicrobials” (IFA v6 for aquaculture)
Added: “authorized by” in certification data
For PHA and GRASP: minor updates
New search option for certification bodies/verification bodies
After having accepted a company as their client, the CB or verification body (VB) will gain access to the company data registered in the GLOBALG.A.P. IT systems as well as to product and certification data (including the certification history). Once a CB/VB is linked to a GLOBALG.A.P. identification number to issue an Option 2/Option 4 certificate, all producer group members linked to this GLOBALG.A.P. identification number will be visible to the CB/VB.
Accordingly, any references to “CB” in sections 3, 4, and 6 only refer to the CBs and/or VBs of which the affected company is a client.
Data access group: benchmarked certification system owner – new definition added
This data access group exclusively represents benchmarked certification system owners (BCSOs). BCSOs are independent organizations which own a scheme/checklist that has been benchmarked by the GLOBALG.A.P. Secretariat and recognized as equivalent to a GLOBALG.A.P. standard or add-on. BCSOs only have access to data related to producers who are certified to their own benchmarked scheme/checklist.
Data access group: public user – clarifications added
Any user of the GLOBALG.A.P. IT systems without a personalized account is considered a “public user” and granted public access rights. Public users may apply for and be given accounts to use certain services, however, their access rights will not be changed.
About historical data
The visibility of the data which is particularly required for integrity purposes, reports, or validations related to the consumer labeling is limited to a certain period of time as specified. This also applies to data related to companies that are suspended and/or have terminated their sublicense and certification/registration agreement(s) with their CB(s)/VB(s).
Historical data is available to BCSOs for only those periods during which the affected company had at least one product certified to the relevant BCSO’s scheme/checklist. Data regarding previous certification to other GLOBALG.A.P. standards and add-ons is not available to BCSOs.
Personal data, if any, will be deleted in accordance with applicable data protection laws notwithstanding the periods defined.
About producer group members/production sites/product handling units (for IFA v6)
Where the standard allows group certification, data is also visible for Option 2 producer groups (certificate holder), but not visible by default for producer group members. Producer group member data is only visible to the respective data access group unless access has been granted by the producer group member. For IFA v6: The producer group controls data access and visibility for the linked producer group member sites and product handling units (PHUs) (including central PHUs) jointly and uniformly.
Clarifications for GRASP
Possible GRASP results: for GRASP v2: GRASP letter of conformance and the results of the GRASP assessment: conformance, non-conformance, and not applicable
For GRASP v2: Public users can retrieve the information via the IFA certificate as it is identical.
For GRASP v2: The GRASP assessment number is not available to public users.
New section for BCSOs (section 6)
Section 3.2 (standard/company data) is copied to section 6; for BCSOs, read Option 3 instead of Option 1 and Option 4 instead of Option 2.
Section 3.3 (product/certification data): If product data is not relevant to a benchmarked scheme/checklist, this data is not displayed at all for the respective scheme/checklist (e.g., parallel ownership).
Audit checklist and results: Available and shared in the GLOBALG.A.P. IT systems if requested by the BCSO and released according to these data access rules as defined in the scheme rules (for benchmarked schemes) or GLOBALG.A.P. normative documents (for benchmarked checklists). If audit checklist data is not available in the GLOBALG.A.P. IT systems, agglomerated audit checklist data will be shared with the GLOBALG.A.P. Secretariat by the BCSO.
Quantity data (availability to market participants): Configuration voluntary for the BCSO. If the BCSO makes it mandatory for their producers, the data will be available to market participants.
The GLOBALG.A.P. Secretariat recommended that CBs communicate this information to their producers.
There have been some updates to the GLOBALG.A.P. product list.
The latest versions of the GLOBALG.A.P. product list (v5.19 and v6.0_Mar24) are available on the GLOBALG.A.P. website:
GLOBALG.A.P. product list v5.19
GLOBALG.A.P. product list v6.0_Mar24
Product name | Chance/Comment | Applicable IFA version: v5 | Applicable IFA version: v6 | ID numbers: FV | ID numbers: PPM | ID numbers: CC | ID numbers: FO | ID numbers: AQ |
---|---|---|---|---|---|---|---|---|
Abacá/ Manila hemp | New product | x | ID 102452 | ID 102449 | ||||
Water chestnut | New product | x | x (only FV) | ID 102449 | ID 102450 |
Added clarification in the GLOBALG.A.P. product list about ornamental classifications (potted plants and plants with/without fruits):
Note 2: If fruit trees (e.g., olive trees, apple trees, etc.) and shrubs (e.g., blueberries, etc.) are produced as ornamentals (to be planted) and not as food (the plant, parts of the plant, or fruit), then these are classified in the product category flowers and ornamentals. If the tree or shrub bears edible parts at the time of sale (e.g., lemon trees), then IFA fruit and vegetable certification applies, and residue testing is required.
Note 3: If potted (or bagged, or naked-root) fruit and vegetable plants are produced for human consumption in the first season of fruiting or harvest (the plant, parts of the plant, or fruit), then IFA fruit and vegetable certification applies, and the products shall be registered according to the edible part of the plant (e.g., tomato, cucumber, strawberry, etc.). If the edible part of the plant is not present at the time of sale, residue testing is not required. If potted (or bagged, or naked-root) plants are intended for ornamental use only, then IFA flower and ornamental certification applies.
The GLOBALG.A.P. educational video series is a free e-learning tool to support stakeholders in understanding risk assessments and their many benefits.
Developed in response to input and questions from our stakeholders, the six-chapter video series is tailored to producers and trainers who want to learn more about on-farm risk assessments. Each chapter tackles a technical topic in less than five minutes, providing key information in a concise and easy-to-understand manner.
Risk assessments – General introduction
Risk assessments – Preparing a risk assessment
Risk assessments – Preharvest water risks and mitigation
Risk assessments – Postharvest water risks and mitigation
Risk assessments – Food fraud risks and mitigation
Risk assessments – Food defense system risks and mitigation
CBs are encouraged to inform their clients directly about the availability of this free resource to support their adoption of GLOBALG.A.P. certification programs. The educational video series is now available on the GLOBALG.A.P. website.
Previously communicated on 10 November 2023
We hereby inform you that we decided to allow a transition period for the full implementation of IT systems’ smart process (i.e., issuing certificates in Validation Service-VS and uploading reports in Audit Online Hub).
GLOBALG.A.P. Secretariat will allow from 1 January 2024 CBs to conduct the entire audit process for all the certification options for Integrated Farm Assurance (IFA) version 6 Smart, IFA v6 GFS and the linked add-ons in the current GLOBALG.A.P. database. This will be allowed for a period and will be terminated with a new announcement by the Secretariat.
During this period, CBs will be able to register, accept and issue IFA v6 certificates for all certification options for the plants and aquaculture scopes, for both IFA v6 Smart and IFA v6 GFS, and for the linked add-ons’ versions in the GLOBALG.A.P. database, issuing their own paper certificates/letter of conformances by using the paper certificate templates that are available in CB Extranet.
CBs may use AOH to upload their checklists (when available) and database as well, following AOH upload rules for legacy process (now applicable for GLOBALG.A.P. database too) for all new standards and add-ons, obligatory from the 1 January 2024. CBs may still use AOH for the standards that do not change on the 1 January 2024, e.g., CoC, IFA v5.4-1 GFS and IFA v5.2 sub scopes CC or PPM.
CBs may choose to issue certificates via the VS or make the certification decision in the current GLOBALG.A.P. database and issue paper certificates.
As already communicated, IFA v5.2 sub scopes fruit and vegetables, flowers and ornamentals, the aquaculture scope, and both IFA v5.2 and IFA v5.3-GFS for hops will be phased out on 31 December 2023 and IFA v6 Smart will become mandatory on 1 January 2024. This date is linked to the audit date and IFA v5.2 and IFA v5.3-GFS for hops certificates issued after these audits will be valid until their “valid to” date, as usual.
Where the purpose of the audit/inspection is the extension or maintenance of valid existing IFA v5.2 certificates, further audits/inspections against this version are allowed in the following situations:
Adding of additional products to the certificate of an IFA v5.2 certified producer/producer group
Adding of new producer group members and/or production sites to the certificate of an IFA v5.2 certified producer group/multisite producer with QMS (within the 10% or above the 10%),
Planning the 10% additional unannounced audits/inspections during the validity of IFA v5.2 certificates, as required in IFA v5.2.
For initial audits where no valid IFA v5.2 certificate already exists no audits against this standard are allowed anymore from 1 January 2024.
Please consider that the first audits of certificate holders (Option 1/Option 2) already certified to IFA v5.2/IFA v5.4-1-GFS against IFA v6 are considered subsequent (recertification) audits. This means that the rule requiring 10% of the subsequent audits to be unannounced applies to these certificate holders and CBs shall consider this new rule in their audit planning for year 2024.
The IFA v5.2 subscopes plant propagation material and combinable crops will remain valid and CB audits may be conducted against them after 1 January 2024.
IFA v5.4-1-GFS for FV and AQ will still be valid, and audits will be possible against this IFA version until GFSI benchmarking is achieved.
IFA v5.4-1-GFS will be replaced by IFA v6 GFS with a transition period allowed after the benchmarking process has successfully finished.
Previously communicated on 27 July 2023
We would like to remind you that CBs will need to get accreditation for IFA v6 at scope level. CBs shall be accredited for IFA v6 Smart by 31 December 2023 at the latest.
If not, after January 2024, the CBs will remain “provisionally approved” and will be allowed to issue a limited number of nonaccredited certificates (to a maximum of 20 producers per scope) starting the calculation from that date.
Both the IFA v6 Smart and IFA v6 GFS editions require accreditation, but both can be achieved in one audit. Accreditation body (AB) witness audits for IFA v6 GFS will also cover IFA v6 Smart.
The GLOBALG.A.P. Secretariat allowed CBs that are provisionally approved for IFA v6 Smart to issue an unlimited number of nonaccredited certificates for IFA v6 Smart until 31 December 2023.
The GLOBALG.A.P. Secretariat does not require a new office assessment from the AB as a precondition for the CB’s accreditation for IFA v6.
The GLOBALG.A.P. Secretariat will be applying for International Accreditation Forum (IAF) evaluation. The IAF mark cannot appear on the certificate until the IAF evaluation has been successfully completed.
If a legal entity requests in parallel IFA v5.4-1-GFS and IFA v6 GFS certification for the same products, the IFA v6 certificate may be issued via Validation Service or GLOBALG.A.P. Database and the IFA v5.4-1-GFS certificate is issued in the GLOBALG.A.P. database.
In such cases (parallel certification of production processes for same products against IFA v5.4-1-GFS and IFA v6 GFS), CBs shall align the valid to date of both certificates (IFA v6 GFS certificate and IFA v5.4-1-GFS), to avoid double charge of GLOBALG.A.P. fees.
The Secretariat will cross check data of GGNs with double certification with same valid to date and will not charge IFA v5.4-1-GFS fees.
When we have parallel IFA v6 Smart and IFA v6 GFS certification or IFA v6 Smart and IFA v5.4-1-GFS certification for the same products, fees will be charged as described in GLOBALG.A.P. general fee table 2021.
IFA for aquaculture: Technical news
We would like to remind CBs of the requirements for postharvest units in IFA v6 for aquaculture. According to the IFA v6 Smart P&C, AQ-Smart 28.06.01 and IFA v6 GFS P&C, AQ-GFS 28.06.01, “For each postharvest unit, the producer has a food safety system in place at the time of the CB audit. This principle and the relevant criteria shall be marked as compliant if the producer has been certified to a GFSI-recognized post-farm gate standard or to a third-party certified Codex Alimentarius-based HACCP system which is accredited at the time of the CB audit.”
AQ 15.01 and FV 14.01 in IFA v6 for aquaculture and fruit and vegetables, respectively, make reference to the completion and signing of the food safety policy declaration.
Please note that the food safety policy declaration was updated and the new version published in November 2024. This document can be downloaded from the GLOBALG.A.P. document center in English and other major languages. It is a policy declaration that addresses elements of a food safety management system and underpins the requirements in the respective P&Cs in IFA v6.
The use of this document as a template is strongly recommended. If this is not feasible, the use of a document similar in terms of content and structure can be used.
The GLOBALG.A.P. Secretariat consulted with the technical committees and certification body committee members to decide the operational items for audits in years 2 and 3. Answers (including comments) from the previous year’s audit will be copied over to the current year’s audit, provided that there is no change, and will still be editable for the CB auditors during the audit.
We are happy to announce that CBs now have access to the list of operational and non-operational items (not the CB audit checklists for years 2 and 3) in the audit method and justification guideline for Integrated Farm Assurance (IFA) standard version 6 Smart for fruit and vegetables and flowers and ornamentals, as well as for IFA v6 Smart/GFS for aquaculture. This list is also available in the CB Extranet for IFA v6 QMS and IFA v6 Smart for hops.
The checklists with operational and non-operational items will only apply for producers that continue with the same CB for recertification. The overall minimum audit duration cannot be reduced. For IFA v6 GFS, the list of operational and non-operational items will become available after GFSI recognition is achieved.
The GLOBALG.A.P. Secretariat consulted with the technical committees and certification body committee members to decide the operational items for audits in years 2 and 3. Answers (including comments) from the previous year’s audit will be copied over to the current year’s audit, provided that there is no change, and will still be editable for the CB auditors during the audit.
We are happy to announce that CBs now have access to the list of operational and non-operational items (not the CB audit checklists for years 2 and 3) in the audit method and justification guideline for Integrated Farm Assurance (IFA) standard version 6 Smart for fruit and vegetables and flowers and ornamentals, as well as for IFA v6 Smart/GFS for aquaculture. This list is also available in the CB Extranet for IFA v6 QMS and IFA v6 Smart for hops.
The checklists with operational and non-operational items will only apply for producers that continue with the same CB for recertification. The overall minimum audit duration cannot be reduced. For IFA v6 GFS, the list of operational and non-operational items will become available after GFSI recognition is achieved.
The GLOBALG.A.P. Secretariat recently published the auditing guideline for IFA v6 Smart/GFS for aquaculture (similar to the IFA v6 Smart audit method and justification guideline for fruit and vegetables) in the document center. You can find this document here.
As communicated in TN 03/2023 (content adapted since TN 03/2023): We would like to inform you that sections 12.3.5 i) and 13.3.5 i), found under section 14, “Additional requirements for IFA v6 GFS,” in the “GLOBALG.A.P. general regulations – Rules for certification bodies,” are to be replaced by the following text:
“The CB shall have in place a procedure to ensure that annually every auditor conducts at least five on-site audits at a number of different producers.
In the case of a CB auditor approved for GFSI-recognized GLOBALG.A.P. standards, the audits required for maintenance of competency shall be against any GLOBALG.A.P. GFSI-benchmarked GLOBALG.A.P. standards with at least one of these annual on-site audit being against the respective GFSI-recognized GLOBALG.A.P. standard.
If this requirement cannot be met, the CB auditors shall carry out 5 on-site audits against any GFSI-approved Certification Programme (see list here), with at least one of these annual on-site audits being against the respective GFSI-recognized GLOBALG.A.P. standard.
For example, a CB auditor may conduct 4 audits to any GFSI-approved Certification Programme and only one audit to IFA v6 GFS to maintain competency for IFA v6 GFS.”
As communicated in TN 03/2023 (content adapted since TN 03/2023): As it reads in the “GLOBALG.A.P. general regulations – Rules for producer groups and multisite producers with QMS,” section 6.1.2.1. e), under section 14, “Additional requirements for IFA v6 GFS,” “at least 25% of the sample shall be randomly selected from the actual number of producer group members/production sites.”
We would like to remind CBs to record in the GLOBALG.A.P. IT systems (Audit Online Hub (AOH)) the producer group members/production sites randomly selected.
Text is also added to section 6.1.2.1 e), under section 14, “Additional requirements for IFA v6 GFS” in the “GLOBALG.A.P. general regulations – Rules for producer groups and multisite producers with QMS” (changes underlined):
“Selection of members/sites shall be based on the risk assessment carried out by the CB. However, at least 25% of the sample shall be randomly selected from the actual number of members/sites.
The risk assessment shall include consideration of the members’/sites’ internal audit program findings and the sites’ specific risks.”
The changes above will be included in the next update of the IFA v6 normative documents (IFA v6.1) and will additionally apply to the Harmonized Produce Safety Standard (HPSS).
We would like to remind the CBs approved for IFA v6 Smart/GFS for aquaculture that there is a relevant change in the food safety requirements for postharvest activities in IFA v6 Smart/GFS for aquaculture, when compared with IFA v5.4-1-GFS for aquaculture:
Food safety system | |||
---|---|---|---|
AQ 28.06.01 | For each postharvest unit, the producer has a food safety system in place at the time of the certification body (CB) audit. | This principle and the relevant criteria shall be marked as compliant if the producer has been certified to a GFSI-recognized post-farm gate standard or to a third-party certified Codex Alimentarius-based HACCP system which is accredited at the time of the CB audit. Note: For transparency purposes, the type of recognition is indicated in the GLOBALG.A.P. IT systems. | Major Must |
In IFA v5.4-1-GFS for aquaculture, the requirement is to have a Codex Alimentarius-based HACCP food safety system documented and implemented, while in IFA v6 Smart/GFS for aquaculture the criteria reads that the third-party certified Codex Alimentarius-based HACCP system shall be accredited.
Transition tool to IFA v6 FO now available
We are pleased to announce the launch of the IFA v6 FO transition tool for the flowers and ornamentals product category, a checklist designed to facilitate a smooth transition from the previous version of IFA v5.2 to IFA v6 Smart FO. This valuable resource will assist producers in aligning their current programs with the updated requirements outlined in the latest version of the standard.
What is the IFA v6 FO transition tool?
The IFA v6 FO transition tool serves as a support tool for producers as they navigate the transition to IFA v6 FO. By mapping the requirements in IFA v5 and IFA v6 FO side by side, this checklist enables producers to identify gaps in their current programs and make necessary adjustments.
What the transition tool is not
It is important to clarify that the use of the IFA v6 FO transition tool is not obligatory. While it displays aligned requirements side by side, it does not provide a comprehensive and detailed list of all the specific changes and differences between the versions. Additionally, it does not highlight specific differences in the requirements. The tool’s primary purpose is to assist producers in aligning their current programs with the new requirements and identifying areas of improvement during the transition process.
How can the transition tool be used?
Producers preparing for IFA v6 FO audits can leverage the tool to ensure a smooth transition. During internal audits, producers can use the tool to respond to the upcoming requirements of IFA v6 FO, identify gaps in their current programs, and take corrective actions to align with the new version. CBs are encouraged to inform their clients directly about the availability of this tool to facilitate a seamless transition.
The IFA v6 transition tool for flowers and ornamentals is now available on the GLOBALG.A.P. website.
Other transition tools to IFA v6 GFS/Smart
As previously communicated in TN 02/2023, the GLOBALG.A.P. Secretariat has launched the IFA v6 transition tools for other scopes/product categories, in order to facilitate a smooth transition from the previous IFA version to IFA v6.
CBs are encouraged to inform their clients directly about the availability of this tool to facilitate a seamless transition. All the IFA v6 transition tools are now available on the GLOBALG.A.P. website.
Fruit and vegetables, GFS edition – English
Fruit and vegetables, GFS edition – Spanish
Fruit and vegetables, Smart edition – English Fruit and vegetables, Smart edition – Spanish
Flowers and ornamentals – English
Herewith we communicate amendment of Rules for GLOBALG.A.P. general regulations – Rules for QMS point 5.2.4 clause 9.1 additional requirements for IFA V6 GFS and GLOBALG.A.P. general regulations–Rules for individual producers, clause 5.2.4 under 8.2 additional requirements for IFA V6 GFS.
CBs shall complete a risk assessment on producers that switch between any GFSI-approved Certification Programmes to any GLOBALG.A.P. GFSI benchmarked standard. This risk assessment shall consider, but shall not be limited to, such aspects as:
Unannounced audits
Suspensions
Withdrawals
Cancellations, etc., by the previous certification programme.
In all cases, audits of producers moving from another GFSI benchmarked Certification Programme to a GLOBALG.A.P. GFSI benchmarked standard shall always be considered as an initial audit and not a subsequent (recertification) audit.
GLOBALG.A.P. general regulations – rules for Certification Bodies clause 8.1.p, GLOBALG.A.P. general regulations – Rules for QMS clause 7.1.d and GLOBALG.A.P. general regulations – Rules for individual producers clause 7.1.d currently read:
“Where the country of destination (as registered in the GLOBALG.A.P. IT systems) includes the USA and/or Canada, the CB shall provide the final CB audit report including the completed audit checklist to the producer, at the latest by the time of the certification decision.”
Here we would like to inform you that the text is amended for IFA v6 GFS as following:
“CBs shall provide the final CB audit report including the completed audit checklist to producers registered for any GLOBALG.A.P. GFSI benchmarked standard, at the latest by the time of the certification decision.”
We would like to inform you that P&Cs FV-GFS 11.01 and of AQ 17.02 are amended to include text:
“Where the root cause is related to significant food safety reasons, the procedure in place shall be implemented and maintained for the determination and implementation of corrective actions. Such actions shall aim to eliminate the cause of a nonconformity to prevent reoccurrence.”
As it reads in Rules for QMS point 6.1.2.1.e for v6 GFS “at least 25% of the sample shall be randomly selected from the actual number of producer group members/production sites.”
We would like to remind CBs to record in GLOBALG.A.P. IT systems (AOH) the producer group members/production sites randomly selected.
IFA v6 National Interpretation Guideline (NIG) templates were updated to include new point 7 about legal identification number. The new NIG templates were launched in document center on 13 September 2023. Registration of legal entities with their unique legal registration number is not mandatory. It is up to the NTWG of each country to decide on mandatory use of this number and include this requirement in the respective country's NIG.
We would like to remind all CBs to use the most recent version of the SLCA (latest version 5) that is available in CB Extranet. Current ones are with separate Privacy Notice except those for North America/Canada.
We have already communicated in the past that IFA v6 certificates issued in GLOBALG.A.P. IT systems following the smart IT process (in Validation Service-VS) are issued in English. CBs can download them and send to the producers. Until more languages are available in VS, CBs may translate the certificate in the local languages, including all information from the English one originated from VS. The same applies for certificates issued in GLOBALG.A.P. database.
A disclaimer shall be added to all certificates issued in VS and translated by the CBs to advise users to refer to the English certificate issued in GLOBALG.A.P. IT systems, that is the original one. CBs shall add in the translated certificate the “Certificate No.” number from the English certificate issued in VS.
CBs shall always share with producers together with the translated version the English certificate issued in GLOBALG.A.P. IT systems.
Previously communicated on 18 and 19 October 2023
As of Saturday morning, 7 October 2023, the security situation has worsened in Israel. The country is in official situation of war. This poses significant risk on producers, certification body auditors and other personnel involved in GLOBALG.A.P. certifications.
GLOBALG.A.P. Secretariat therefore is from now offering the possibility to activate the emergency procedure for certificate validity extension for a maximum period of six months.
In addition, the certification bodies that are not able to conduct an on-site inspection/audit due to the current official travel restrictions and state of emergency circumstances (“force majeure”) in Israel (including Israel and Golan Heights -Israel; Israel and West Bank -Israel) , Lebanon and in the Palestinian Territory may conduct the inspection/audit remotely following the GLOBALG.A.P. Remote Procedure (ver. 1.3). The time frame for the application of GLOBALG.A.P. Remote Procedure starts with immediate effect and will terminate by 31 December 2023. If further extension of the validity of application of the procedure will be required, it will be communicated in a timely manner by the Secretariat.
GLOBALG.A.P. Remote Procedure was introduced as a response to the coronavirus crisis and was published in May 2020. The GLOBALG.A.P. Remote Procedure solution is applicable to the majority of GLOBALG.A.P. standards and add-ons, with the exception of GFSI-recognized editions.
The GLOBALG.A.P. Secretariat will continue to communicate updates on this topic and remains available to respond to questions or concerns. In the meantime, we call for peace.
IFA for fruit and vegetables: Technical news
According to version 6 of “GLOBALG.A.P. general regulations – Rules for parallel ownership,” having IFA v6 Smart and IFA v6 GFS certification at the same time is not considered parallel ownership.
However, we would like to clarify that whenever the GLOBALG.A.P. identification number is used for products originating from production processes certified to IFA v6 GFS the GFS extension shall be used (e.g., GGN_1234567890123_GFS).
After feedback we received from our stakeholders, we would like to issue clarifications on FV‑Smart 30.01.01 and FV-GFS 30.01.01 about the need and frequency for water analysis.
This analysis, taking into account physical, chemical, and microbiological contamination, shall be based on a risk assessment as described in the respective P&Cs.
The required frequency for water analysis is at least once per year for preharvest water that comes into contact with the edible part of the registered product.
This means that, based on a documented risk assessment, it could be acceptable to omit water analysis for microbiological parameters, for e.g., potato under drip irrigation that is peeled and always cooked prior to consumption. This being said, depending on, e.g., the water source, other parameters such as heavy metals or other contaminants, might still be relevant.
The GLOBALG.A.P. Secretariat does not specify thresholds for microbiological/physical/chemical parameters for preharvest water. However, water that makes contact with the edible part of the product during harvest and postharvest, shall be analyzed and shall meet microbial standards equivalent to drinking water.
“GLOBALG.A.P. general regulations – Rules for plants,” section 2.3 f) shall be corrected as follows:
“If the product handling unit (PHU) already has a post-farm gate food safety certification recognized by GFSI for scope BIII ‘Preprocess handling of plant products’ (www.mygfsi.com), the GLOBALG.A.P. approved CB auditor shall audit, as a minimum, segregation and traceability, postharvest treatments, if applicable, and the sections listed below for Option 2 and Option 1, respectively. In cases of doubt, the CB can reaudit all other applicable P&Cs.
For Option 2:
In addition to the P&Cs on the “PHU-FV” tab of the IFA v6 Smart and the IFA v6 GFS QMS checklists, the CB auditor shall audit the following sections as a minimum:
FV 20 Worker’s health, safety and welfare
FV 22 Biodiversity and habitats
FV 23 Energy efficiency
FV 27 Genetically modified organisms
FV 32 Plant protection products
All the P&Cs on the “QMS” tab of the IFA v6 Smart and the IFA v6 GFS QMS checklists shall still be audited (including section QMS 06, “Product traceability and segregation,” which is implemented for the QMS and for the central PHU), regardless of any GFSI-recognized post-farm gate food safety certification of the PHU.
For Option 1:
The P&Cs of the IFA v6 for fruit and vegetables CB audit checklist that the CB auditor shall audit, as a minimum, are the following:
FV 06 Traceability
FV 07 Parallel ownership, traceability, and segregation
FV 08 Mass balance
FV 18 GLOBALG.A.P. status
FV 20 Worker`s health, safety and welfare
FV 22 Biodiversity and habitats
FV 23 Energy efficiency
FV 27 Genetically modified organisms
FV 24 Greenhouse gases and climate change
FV 32 Plant protection products”
Please keep in mind that scope BII “Farming of grains and pulses” is not included in “GLOBALG.A.P. general regulations – Rules for plants” anymore.
In the aquaculture scope, all PHUs and all the P&Cs applicable to PHUs shall be audited. In the IFA v6 Smart standard for flowers and ornamentals, sampling of the central PHUs is possible as described in the GLOBALG.A.P. general regulations, and all the P&Cs applicable to central PHUs shall be audited.
AQ 15.01 and FV 14.01 in IFA v6 for aquaculture and fruit and vegetables, respectively, make reference to the completion and signing of the food safety policy declaration.
Please note that the food safety policy declaration was updated and the new version published in November 2024. This document can be downloaded from the GLOBALG.A.P. document center in English and other major languages. It is a policy declaration that addresses elements of a food safety management system and underpins the requirements in the respective P&Cs in IFA v6.
The use of this document as a template is strongly recommended. If this is not feasible, the use of a document similar in terms of content and structure can be used.
In IFA v6 for fruit and vegetables, FV 12.01 makes reference to laboratory testing that shall occur in a manner consistent with the industry requirements. Please note that this P&C relates to the analysis of only the parameters impacting food safety. Where the analysis of samples may relate to parameters other than food safety (e.g., soil analysis for soil fertility programs), the requirement in FV 12.01 does not apply.
This P&C remains valid for the analysis of samples conducted by a laboratory for physical, chemical, and microbiological contamination related to the food safety of the product. This could include e.g., water, soil, product, and environmental monitoring samples.
As part of our ongoing commitment to quality and compliance, we want to provide some friendly guidance on sample size requirements for residue monitoring. We kindly ask CBs to address this topic with all relevant parties. Our IFA v6 standard (Smart and GFS editions) requires verification of the maximum residue limits (MRLs). The producer (group) can take its own MRL samples or make use of an approved residue monitoring system (RMS). Furthermore, collecting MRL samples shall follow best practices and legal requirements. On a global level, the Food and Agriculture Organization (FAO) has published the guideline CAC/GL 33, “Recommended methods of sampling for the determination of pesticide residues for compliance with MRLs.” In the European Union, this guideline is implemented in the EU Commission Directive 2002/63/EC, establishing sampling methods for the official control of pesticide residues in and on products of plant and animal origin within the European Union.
Why is this important?
Lately, we have had to reject a large number of MRL results due to insufficient sample weight. This causes frustration and additional costs for producers, traders, and RMS operators. In order to prevent these additional costs and resulting frustration, we want to remind all parties about the sampling regulations stipulated by the FAO and the European Union.
Accurate sampling ensures that our residue monitoring is both reliable and consistent. By adhering to the specified sample sizes, we can confidently assess pesticide residue levels, ensuring they meet safety standards and maintain consumer trust.
Key points to remember:
1. Sample weight: For most crops, the aggregate sample should weigh at least 1 kilogram.
Please familiarize yourself with Table 4 of EU Commission Directive 2002/63/EC. You can find it in English, Spanish, German, Italian, Dutch, French, and other European languages.
This aggregate sample is composed of several primary samples taken from different points within a lot to provide a representative assessment.
2. Documentation: To maintain transparency and accuracy:
Clearly state the total weight of the aggregate sample in your lab results.
Alternatively, include a photograph of the sample.
A practical example:
Imagine you’re sampling apples:
Primary samples: You might collect 10 apples from various parts of a shipment.
Aggregate sample: These apples together form your aggregate sample. If each apple weighs approximately 150 grams, your total sample would be 1.5 kilograms, meeting the requirement.
By following these steps, we ensure that our sampling methods align with the directive’s guidelines, leading to more robust and trustworthy results.
If you have any questions or need further clarification, please don’t hesitate to reach out.
The GLOBALG.A.P. Secretariat consulted with the technical committees and certification body committee members to decide the operational items for audits in years 2 and 3. Answers (including comments) from the previous year’s audit will be copied over to the current year’s audit, provided that there is no change, and will still be editable for the CB auditors during the audit.
We are happy to announce that CBs now have access to the list of operational and non-operational items (not the CB audit checklists for years 2 and 3) in the audit method and justification guideline for Integrated Farm Assurance (IFA) standard version 6 Smart for fruit and vegetables and flowers and ornamentals, as well as for IFA v6 Smart/GFS for aquaculture. This list is also available in the CB Extranet for IFA v6 QMS and IFA v6 Smart for hops.
The checklists with operational and non-operational items will only apply for producers that continue with the same CB for recertification. The overall minimum audit duration cannot be reduced. For IFA v6 GFS, the list of operational and non-operational items will become available after GFSI recognition is achieved.
The GLOBALG.A.P. Secretariat consulted with the technical committees and certification body committee members to decide the operational items for audits in years 2 and 3. Answers (including comments) from the previous year’s audit will be copied over to the current year’s audit, provided that there is no change, and will still be editable for the CB auditors during the audit.
We are happy to announce that CBs now have access to the list of operational and non-operational items (not the CB audit checklists for years 2 and 3) in the audit method and justification guideline for Integrated Farm Assurance (IFA) standard version 6 Smart for fruit and vegetables and flowers and ornamentals, as well as for IFA v6 Smart/GFS for aquaculture. This list is also available in the CB Extranet for IFA v6 QMS and IFA v6 Smart for hops.
The checklists with operational and non-operational items will only apply for producers that continue with the same CB for recertification. The overall minimum audit duration cannot be reduced. For IFA v6 GFS, the list of operational and non-operational items will become available after GFSI recognition is achieved.
As communicated in TN 03/2023 (content adapted since TN 03/2023): We would like to inform you that sections 12.3.5 i) and 13.3.5 i), found under section 14, “Additional requirements for IFA v6 GFS,” in the “GLOBALG.A.P. general regulations – Rules for certification bodies,” are to be replaced by the following text:
“The CB shall have in place a procedure to ensure that annually every auditor conducts at least five on-site audits at a number of different producers.
In the case of a CB auditor approved for GFSI-recognized GLOBALG.A.P. standards, the audits required for maintenance of competency shall be against any GLOBALG.A.P. GFSI-benchmarked GLOBALG.A.P. standards with at least one of these annual on-site audit being against the respective GFSI-recognized GLOBALG.A.P. standard.
If this requirement cannot be met, the CB auditors shall carry out 5 on-site audits against any GFSI-approved Certification Programme (see list here), with at least one of these annual on-site audits being against the respective GFSI-recognized GLOBALG.A.P. standard.
For example, a CB auditor may conduct 4 audits to any GFSI-approved Certification Programme and only one audit to IFA v6 GFS to maintain competency for IFA v6 GFS.”
As communicated in TN 03/2023 (content adapted since TN 03/2023): As it reads in the “GLOBALG.A.P. general regulations – Rules for producer groups and multisite producers with QMS,” section 6.1.2.1. e), under section 14, “Additional requirements for IFA v6 GFS,” “at least 25% of the sample shall be randomly selected from the actual number of producer group members/production sites.”
We would like to remind CBs to record in the GLOBALG.A.P. IT systems (Audit Online Hub (AOH)) the producer group members/production sites randomly selected.
Text is also added to section 6.1.2.1 e), under section 14, “Additional requirements for IFA v6 GFS” in the “GLOBALG.A.P. general regulations – Rules for producer groups and multisite producers with QMS” (changes underlined):
“Selection of members/sites shall be based on the risk assessment carried out by the CB. However, at least 25% of the sample shall be randomly selected from the actual number of members/sites.
The risk assessment shall include consideration of the members’/sites’ internal audit program findings and the sites’ specific risks.”
The changes above will be included in the next update of the IFA v6 normative documents (IFA v6.1) and will additionally apply to the Harmonized Produce Safety Standard (HPSS).
We would like to communicate that P&C 30.05.01 in IFA v6 for fruit and vegetables has been adapted to include the consideration of preharvest water analysis, and to add clarification for municipal water use (changes underlined):
“All pre- and postharvest water shall be analyzed for food safety (physical, chemical, and microbiological contamination) at a frequency consistent with the risk assessment and current sector-specific standards or relevant regulations. Water analysis shall be part of the water management plan and completed at least once per year, or more frequently if required by the risk assessment (e.g., in controlled environment agriculture (CEA) production).
A minimum of one analysis per season or certification cycle shall be required on water that comes into contact with products during pre- and postharvest activities, with samples taken as near the point of application as possible. A minimum of one analysis shall be required even when using municipal water sources.
The water analysis shall reflect the nature and extent of the water system, the scope of production (type of product, applications, harvesting, handling, water sources, etc.). Where different water sources are used, they shall each be sampled. Samples shall be taken from locations that are representative of the water source, usually as close to the point of application as possible. Analysis shall be performed during the time of water use on products and during the period of highest risk.
There shall be a documented procedure for water analysis, including:
Frequency of sampling
Person responsible for sampling
Method of sample collection
Laboratory analyzing the samples
Location sampled
Records of all analysis shall be maintained, and in cases where municipal water or a group water scheme is used during pre- and postharvest activities, the results of the water analysis provided by the water supplier (municipality or group water scheme operator) may be used as evidence during the audit process. (Group water schemes are those operating in rural areas, outside the scope of urban public mains systems. They can be public or private, depending on whether the water comes from the public mains or a private source such as a lake, river, well, or spring.) However, the producer and/or product handling unit (PHU) must still consider the risk of contamination occurring between the entry point to the farm and/or PHU and the point of use. These may include distribution systems, pipes, storage points of water, etc. In cases where a risk of contamination is identified, at a minimum, an annual water analysis (in addition to the results of the water analysis provided by the water supplier) shall be required by the producer and/or PHU to confirm that the water meets the minimum requirements as per the risk assessment.”
The changes above will be included in the next update of the IFA v6 normative documents (IFA v6.1).
Previously communicated on 8 May 2024
We would like to inform you that in the residue monitoring system (RMS) checklist version 6.0_Sep22, “Definitions” tab, changes have been made to point 6 under:
“Criteria 2.4 and 2.7– Minimum number of samples for the production of fruit and vegetables, combinable crops, tea, and hops: Rules for level of sampling”
“Criteria 2.5 and 2.7– Minimum number of samples for the traded fruit and vegetables, combinable crops, tea, and hops: Rules for the level of sampling”
The present text in point 6 reads: “If the RMS operator is able to demonstrate compliance to the standard level in the two years prior to the year of implementation of RMS v6, the reduced level applies.”
The new text for point 6 reads: “If the RMS operator is able to demonstrate compliance to the reduced level in the two years prior to the year of implementation of RMS v6, the reduced level applies. If the RMS operator is not able to demonstrate compliance to the reduced level, the standard level applies.”
This updated text for point 6 is applicable from the publication date of this communication. The text that appears in point 6 in the “Definitions” tab will be updated in the next version of the RMS checklist.
Here we would like to share further clarification about the rule presented in the IFA v6 residue monitoring system (RMS) checklist:
“In the framework of GLOBALG.A.P. Chain of Custody (CoC) certification for the plants scope, the supply chain actor (e.g., trader) has the option to participate in an RMS audited by a CB or to operate their own RMS. An RMS in the framework of CoC certification means the additional monitoring of maximum residue limits (MRLs) and does not replace the requirement for producers to demonstrate compliance with the P&Cs referring to residue analysis in the framework of IFA certification. Operating an RMS or participating in an RMS is not a requirement for CoC certification” (see the IFA v6 RMS checklist, “Rules” tab, “RULES FOR THE RESIDUE MONITORING SYSTEM”).
Where the supply chain actors (e.g., traders) offer an RMS for their suppliers to demonstrate compliance with P&C FV-Smart/GFS 32.07.02, this RMS shall be in compliance with IFA v6 RMS checklist requirements (site-based sampling). This is not a mandatory part of CoC certification.
Where the supply chain actors (e.g., traders) operate an RMS for their traded products, the samples are volume-based (tonnage) and the monitoring is an additional assurance for markets of destination. This is not a mandatory part of CoC certification. This does not replace the requirement for compliance with P&C FV-Smart/GFS 32.07.02.
Transition tool to IFA v6 FO now available
We are pleased to announce the launch of the IFA v6 FO transition tool for the flowers and ornamentals product category, a checklist designed to facilitate a smooth transition from the previous version of IFA v5.2 to IFA v6 Smart FO. This valuable resource will assist producers in aligning their current programs with the updated requirements outlined in the latest version of the standard.
What is the IFA v6 FO transition tool?
The IFA v6 FO transition tool serves as a support tool for producers as they navigate the transition to IFA v6 FO. By mapping the requirements in IFA v5 and IFA v6 FO side by side, this checklist enables producers to identify gaps in their current programs and make necessary adjustments.
What the transition tool is not
It is important to clarify that the use of the IFA v6 FO transition tool is not obligatory. While it displays aligned requirements side by side, it does not provide a comprehensive and detailed list of all the specific changes and differences between the versions. Additionally, it does not highlight specific differences in the requirements. The tool’s primary purpose is to assist producers in aligning their current programs with the new requirements and identifying areas of improvement during the transition process.
How can the transition tool be used?
Producers preparing for IFA v6 FO audits can leverage the tool to ensure a smooth transition. During internal audits, producers can use the tool to respond to the upcoming requirements of IFA v6 FO, identify gaps in their current programs, and take corrective actions to align with the new version. CBs are encouraged to inform their clients directly about the availability of this tool to facilitate a seamless transition.
The IFA v6 transition tool for flowers and ornamentals is now available on the GLOBALG.A.P. website.
Other transition tools to IFA v6 GFS/Smart
As previously communicated in TN 02/2023, the GLOBALG.A.P. Secretariat has launched the IFA v6 transition tools for other scopes/product categories, in order to facilitate a smooth transition from the previous IFA version to IFA v6.
CBs are encouraged to inform their clients directly about the availability of this tool to facilitate a seamless transition. All the IFA v6 transition tools are now available on the GLOBALG.A.P. website.
Fruit and vegetables, GFS edition – English
Fruit and vegetables, GFS edition – Spanish
Fruit and vegetables, Smart edition – English Fruit and vegetables, Smart edition – Spanish
Flowers and ornamentals – English
FV 07.02 reads that: | |
---|---|
The GLOBALG.A.P. Number (GGN) is indicated on all final products originating from certified production processes when registered for parallel ownership. | Where the producer is registered for parallel ownership (i.e., where products originating from certified and noncertified production processes are owned in parallel by one legal entity), all products originating from certified production processes packed in final consumer packaging (either on the farm or after product handling) shall be identified with a GGN. It can be the GGN of the Option 2 producer group, the GGN of the producer group member, both GGNs, or the GGN of the Option 1 individual producer. The GGN shall not be used to label products originating from noncertified production processes. |
This P&C can be non-applicable (N/A) when:
The producer/the producer group only owns GLOBALG.A.P. products (no parallel ownership)
or
When there is a written agreement available between the producer/the producer group and the buyer not to use the GGN on producer’s final product packaging
or
When there is a market label specification that prevents the producer/producer group from using the GGN on the producer’s final product packaging
In all cases where the GGN is not used on final product when there is parallel ownership, there shall be at minimum a system in place to identify the product originating from certified production. There shall be written information in place between the buyer and the producer/producer group which explains the system. All agreements and communication shall be documented and available during the CB audits.
GLOBALG.A.P. general regulations – rules for Certification Bodies clause 8.1.p, GLOBALG.A.P. general regulations – Rules for QMS clause 7.1.d and GLOBALG.A.P. general regulations – Rules for individual producers clause 7.1.d currently read:
“Where the country of destination (as registered in the GLOBALG.A.P. IT systems) includes the USA and/or Canada, the CB shall provide the final CB audit report including the completed audit checklist to the producer, at the latest by the time of the certification decision.”
Here we would like to inform you that the text is amended for IFA v6 GFS as following:
“CBs shall provide the final CB audit report including the completed audit checklist to producers registered for any GLOBALG.A.P. GFSI benchmarked standard, at the latest by the time of the certification decision.”
Herewith we communicate amendment of Rules for GLOBALG.A.P. general regulations – Rules for QMS point 5.2.4 clause 9.1 additional requirements for IFA V6 GFS and GLOBALG.A.P. general regulations–Rules for individual producers, clause 5.2.4 under 8.2 additional requirements for IFA V6 GFS.
CBs shall complete a risk assessment on producers that switch between any GFSI-approved Certification Programmes to any GLOBALG.A.P. GFSI benchmarked standard. This risk assessment shall consider, but shall not be limited to, such aspects as:
Unannounced audits
Suspensions
Withdrawals
Cancellations, etc., by the previous certification programme.
In all cases, audits of producers moving from another GFSI benchmarked Certification Programme to a GLOBALG.A.P. GFSI benchmarked standard shall always be considered as an initial audit and not a subsequent (recertification) audit.
We would like to inform you that P&Cs FV-GFS 11.01 and of AQ 17.02 are amended to include text:
“Where the root cause is related to significant food safety reasons, the procedure in place shall be implemented and maintained for the determination and implementation of corrective actions. Such actions shall aim to eliminate the cause of a nonconformity to prevent reoccurrence.”
IFA for flowers and ornamentals: Technical news
In the floriculture sector, the Floriculture Sustainability Initiative (FSI) plays a key role in some supply chains.
Producers in the Global North are required by FSI to be certified to:
a) A standard for good agricultural practices (G.A.P.), e.g., IFA v6 Smart for flowers and ornamentals
AND
b) An environmental registration solution, like the IDA add-on for plants v1.1.
Producers in the Global South are additionally required to be certified to a social standard.
This year in Q3, the GLOBALG.A.P. Secretariat will launch the new Social Responsibility standard for flowers and ornamentals to meet the requirements of the FSI “Basket of Standards.” For more information, see GLOBALG.A.P. solutions soon to cover all three FSI “Basket of Standards” scopes.
The GLOBALG.A.P. Secretariat consulted with the technical committees and certification body committee members to decide the operational items for audits in years 2 and 3. Answers (including comments) from the previous year’s audit will be copied over to the current year’s audit, provided that there is no change, and will still be editable for the CB auditors during the audit.
We are happy to announce that CBs now have access to the list of operational and non-operational items (not the CB audit checklists for years 2 and 3) in the audit method and justification guideline for Integrated Farm Assurance (IFA) standard version 6 Smart for fruit and vegetables and flowers and ornamentals, as well as for IFA v6 Smart/GFS for aquaculture. This list is also available in the CB Extranet for IFA v6 QMS and IFA v6 Smart for hops.
The checklists with operational and non-operational items will only apply for producers that continue with the same CB for recertification. The overall minimum audit duration cannot be reduced. For IFA v6 GFS, the list of operational and non-operational items will become available after GFSI recognition is achieved.
Transition tool to IFA v6 FO now available
We are pleased to announce the launch of the IFA v6 FO transition tool for the flowers and ornamentals product category, a checklist designed to facilitate a smooth transition from the previous version of IFA v5.2 to IFA v6 Smart FO. This valuable resource will assist producers in aligning their current programs with the updated requirements outlined in the latest version of the standard.
What is the IFA v6 FO transition tool?
The IFA v6 FO transition tool serves as a support tool for producers as they navigate the transition to IFA v6 FO. By mapping the requirements in IFA v5 and IFA v6 FO side by side, this checklist enables producers to identify gaps in their current programs and make necessary adjustments.
What the transition tool is not
It is important to clarify that the use of the IFA v6 FO transition tool is not obligatory. While it displays aligned requirements side by side, it does not provide a comprehensive and detailed list of all the specific changes and differences between the versions. Additionally, it does not highlight specific differences in the requirements. The tool’s primary purpose is to assist producers in aligning their current programs with the new requirements and identifying areas of improvement during the transition process.
How can the transition tool be used?
Producers preparing for IFA v6 FO audits can leverage the tool to ensure a smooth transition. During internal audits, producers can use the tool to respond to the upcoming requirements of IFA v6 FO, identify gaps in their current programs, and take corrective actions to align with the new version. CBs are encouraged to inform their clients directly about the availability of this tool to facilitate a seamless transition.
The IFA v6 transition tool for flowers and ornamentals is now available on the GLOBALG.A.P. website.
Other transition tools to IFA v6 GFS/Smart
As previously communicated in TN 02/2023, the GLOBALG.A.P. Secretariat has launched the IFA v6 transition tools for other scopes/product categories, in order to facilitate a smooth transition from the previous IFA version to IFA v6.
CBs are encouraged to inform their clients directly about the availability of this tool to facilitate a seamless transition. All the IFA v6 transition tools are now available on the GLOBALG.A.P. website.
Fruit and vegetables, GFS edition – English
Fruit and vegetables, GFS edition – Spanish
Fruit and vegetables, Smart edition – English Fruit and vegetables, Smart edition – Spanish
Flowers and ornamentals – English
IFA for plant propagation material: Technical news
Previously communicated on 8 July 2025.
The normative documents for Integrated Farm Assurance (IFA) version 6 for the plant propagation material (PPM) and combinable crops (CC) product categories were published on 8 July 2025 on the GLOBALG.A.P. website and will become valid (i.e., it will be possible to audit and certify against this new version) from 1 December 2025. PPM and CC are only available in IFA v6 Smart. The normative documents are available in the GLOBALG.A.P. document center in English. Spanish translations are forthcoming. The new IFA v6 PPM and CC standards shall only be combined with the add-on versions that are linked to IFA v6.
There will be a transition period until 30 April 2026 during which audits against IFA v5.2 PPM and CC can still be conducted. However, individual producers and producer groups seeking certification against IFA PPM and/or CC with audits planned after 1 December 2025 are advised to register only for IFA v6 Smart.
IFA v6 PPM and CC will replace IFA v5.2 PPM and CC from 1 May 2026. After this date, it will no longer be possible to audit against IFA v5.2 PPM and CC. All IFA v5.2 PPM and CC certificates issued during the transition period will remain valid up to 30 April 2027 (including any extensions taking place).
Where the purpose of the audit/inspection is the extension or maintenance of valid existing IFA v5.2 PPM and CC certificates, further audits/inspections against this version will be allowed after 1 May 2026 only in the following situations:
Surveillance audits against IFA v5.2 PPM and/or CC during the certificate validity of Option 2 producer groups/Option 1 multisite producers with a quality management system (QMS)
Addition of further products to the currently valid IFA v5.2 PPM and/or CC certificate of a producer/producer group
Addition of new producer group members and/or production sites to the currently valid IFA v5.2 PPM and/or CC certificate of an Option 2 producer group/Option 1 multisite producer with QMS (within the 10% or above the 10%)
In all the above cases, the certificate cannot have a valid to date later than 30 April 2027. It is not possible to extend the validity of IFA v5.2 PPM and CC certificates later than 30 April 2027.
Notify your clients
Please inform your clients that upcoming IFA PPM and CC audits after 1 May 2026 shall be against IFA v6 Smart. Please also inform them that they can already start using this new version from 1 December 2025 for their internal audits/self-assessments or for their CB audits.
CB approval and accreditation for IFA v6 Smart
There will be no new extension of the current license and certification agreement v5, as IFA v6 Smart for plants already covers PPM and CC.
CBs do not need additional accreditation for IFA v6 PPM and/or CC, as IFA v6 Smart accreditation is at scope level, here for the plants scope.
CBs shall be accredited for the IFA v6 Smart plants scope at the time they start CB audits against IFA v6 PPM and/or CC.
However, some ABs may ask you to submit evidence about how the changes related to the new IFA v6 PPM and CC standards are addressed.
CBs and in-house trainers (IHTs) already approved for IFA v6 Smart for plants
All CBs currently approved for IFA v6 Smart for plants, shall send their IHTs for IFA v6 for plants to the additional IFA v6 for plants IHT training offered by the GLOBALG.A.P. Secretariat, and the IHTs shall successfully complete and pass the additional IHT test for PPM and CC.
This additional IHT training and passing the additional IHT test shall take place before the replacement date, that is, 1 May 2026.
These additional IHT trainings for IFA v6 for plants, will become available in the GLOBALG.A.P. CB Academy by the end of 2025. IHTs can search for all available CB trainings in the GLOBALG.A.P. CB Academy by registering with their credentials.
CB auditors already approved for IFA v6 Smart for plants
All CB auditors currently approved for IFA v6 Smart for plants, shall be trained by the IHT internally in their CB and successfully complete and pass the additional online test for IFA v6 for plants focusing on the PPM and CC product categories. This online test shall be conducted withinone month of its becoming available in the GLOBALG.A.P. CB Academy in the working language of the CB auditor.
Failure to attend the additional IHT training for the IFA v6 Smart plants scope PPM/CC will result in the CB being blocked in the GLOBALG.A.P. IT platform and not being able to conduct audits against IFA v6 PPM and CC.
New CBs: IHT and CB auditor training requirements
CBs and CB auditors that are approved for IFA v5.2 PPM and/or CC but who are not approved for IFA v6 Smart for plants shall follow the CB approval process and the CB auditor sign-off process as described in version 6 of “GLOBALG.A.P. general regulations – Rules for certification bodies.”
What is new in IFA v6 PPM and CC?
Plant propagation material version 6
IFA v6 PPM is now in general alignment with other product categories of the IFA v6 Smart standard in terms of updated environmental topics and metrics and workers’ health and safety. The PPM product category has been delinked from food safety, which means there are no principles and criteria (P&Cs) to ensure food safety. As a consequence, products originating from production processes that are certified to IFA v6 PPM cannot claim food safety, and where this was the intention, IFA v6 for fruit and vegetables (FV) should be used together with IFA v6 PPM.
In addition to good agricultural practices which address environmental protection and workers’ health and safety, the PPM product category specifically focuses on the traceability of the propagation material and the plant health of the propagation material obtained.
Most P&Cs in IFA v6 PPM are shared with IFA v6 Smart FV and IFA v6 for flowers and ornamentals (FO). IFA v6 PPM has 33 propagation-specific topics not contained in IFA v6 Smart FV and 26 propagation-specific topics not contained in IFA v6 FO.
Similar to IFA v6 Smart FV and IFA v6 FO, IFA v6 PPM sees a reduction in the number of P&Cs originating mainly from merging P&Cs and from deletions.
A new P&C is introduced and opens the P&C document, requiring producer awareness of the risks (not necessarily a documented risk assessment) and critical production steps for controlling the traceability, origin, and plant health of the propagation material.
Overall, the specific propagation P&Cs were updated and adjusted based on input from stakeholders, e.g., the IFA PPM certificate holders.
Combinable crops version 6
IFA v6 CC is now in general alignment with other product categories of the IFA v6 Smart standard and mostly with IFA v6 Smart FV. Topics such as environmental responsibility and workers’ health and safety have been brought in line, as well as other elements such as food safety, production processes, traceability, etc.
P&Cs specific to the postharvest handling and long-term storage of combinable crops have also been addressed in this new version.
IFA for hops: Technical news
News items from technical news editions published in Q4 2023 and beyond are published here. Please check the document center for technical news editions published prior to this.
IFA for combinable crops: Technical news
Previously communicated on 8 July 2025.
The normative documents for Integrated Farm Assurance (IFA) version 6 for the plant propagation material (PPM) and combinable crops (CC) product categories were published on 8 July 2025 on the GLOBALG.A.P. website and will become valid (i.e., it will be possible to audit and certify against this new version) from 1 December 2025. PPM and CC are only available in IFA v6 Smart. The normative documents are available in the GLOBALG.A.P. document center in English. Spanish translations are forthcoming. The new IFA v6 PPM and CC standards shall only be combined with the add-on versions that are linked to IFA v6.
There will be a transition period until 30 April 2026 during which audits against IFA v5.2 PPM and CC can still be conducted. However, individual producers and producer groups seeking certification against IFA PPM and/or CC with audits planned after 1 December 2025 are advised to register only for IFA v6 Smart.
IFA v6 PPM and CC will replace IFA v5.2 PPM and CC from 1 May 2026. After this date, it will no longer be possible to audit against IFA v5.2 PPM and CC. All IFA v5.2 PPM and CC certificates issued during the transition period will remain valid up to 30 April 2027 (including any extensions taking place).
Where the purpose of the audit/inspection is the extension or maintenance of valid existing IFA v5.2 PPM and CC certificates, further audits/inspections against this version will be allowed after 1 May 2026 only in the following situations:
Surveillance audits against IFA v5.2 PPM and/or CC during the certificate validity of Option 2 producer groups/Option 1 multisite producers with a quality management system (QMS)
Addition of further products to the currently valid IFA v5.2 PPM and/or CC certificate of a producer/producer group
Addition of new producer group members and/or production sites to the currently valid IFA v5.2 PPM and/or CC certificate of an Option 2 producer group/Option 1 multisite producer with QMS (within the 10% or above the 10%)
In all the above cases, the certificate cannot have a valid to date later than 30 April 2027. It is not possible to extend the validity of IFA v5.2 PPM and CC certificates later than 30 April 2027.
Notify your clients
Please inform your clients that upcoming IFA PPM and CC audits after 1 May 2026 shall be against IFA v6 Smart. Please also inform them that they can already start using this new version from 1 December 2025 for their internal audits/self-assessments or for their CB audits.
CB approval and accreditation for IFA v6 Smart
There will be no new extension of the current license and certification agreement v5, as IFA v6 Smart for plants already covers PPM and CC.
CBs do not need additional accreditation for IFA v6 PPM and/or CC, as IFA v6 Smart accreditation is at scope level, here for the plants scope.
CBs shall be accredited for the IFA v6 Smart plants scope at the time they start CB audits against IFA v6 PPM and/or CC.
However, some ABs may ask you to submit evidence about how the changes related to the new IFA v6 PPM and CC standards are addressed.
CBs and in-house trainers (IHTs) already approved for IFA v6 Smart for plants
All CBs currently approved for IFA v6 Smart for plants, shall send their IHTs for IFA v6 for plants to the additional IFA v6 for plants IHT training offered by the GLOBALG.A.P. Secretariat, and the IHTs shall successfully complete and pass the additional IHT test for PPM and CC.
This additional IHT training and passing the additional IHT test shall take place before the replacement date, that is, 1 May 2026.
These additional IHT trainings for IFA v6 for plants, will become available in the GLOBALG.A.P. CB Academy by the end of 2025. IHTs can search for all available CB trainings in the GLOBALG.A.P. CB Academy by registering with their credentials.
CB auditors already approved for IFA v6 Smart for plants
All CB auditors currently approved for IFA v6 Smart for plants, shall be trained by the IHT internally in their CB and successfully complete and pass the additional online test for IFA v6 for plants focusing on the PPM and CC product categories. This online test shall be conducted withinone month of its becoming available in the GLOBALG.A.P. CB Academy in the working language of the CB auditor.
Failure to attend the additional IHT training for the IFA v6 Smart plants scope PPM/CC will result in the CB being blocked in the GLOBALG.A.P. IT platform and not being able to conduct audits against IFA v6 PPM and CC.
New CBs: IHT and CB auditor training requirements
CBs and CB auditors that are approved for IFA v5.2 PPM and/or CC but who are not approved for IFA v6 Smart for plants shall follow the CB approval process and the CB auditor sign-off process as described in version 6 of “GLOBALG.A.P. general regulations – Rules for certification bodies.”
What is new in IFA v6 PPM and CC?
Plant propagation material version 6
IFA v6 PPM is now in general alignment with other product categories of the IFA v6 Smart standard in terms of updated environmental topics and metrics and workers’ health and safety. The PPM product category has been delinked from food safety, which means there are no principles and criteria (P&Cs) to ensure food safety. As a consequence, products originating from production processes that are certified to IFA v6 PPM cannot claim food safety, and where this was the intention, IFA v6 for fruit and vegetables (FV) should be used together with IFA v6 PPM.
In addition to good agricultural practices which address environmental protection and workers’ health and safety, the PPM product category specifically focuses on the traceability of the propagation material and the plant health of the propagation material obtained.
Most P&Cs in IFA v6 PPM are shared with IFA v6 Smart FV and IFA v6 for flowers and ornamentals (FO). IFA v6 PPM has 33 propagation-specific topics not contained in IFA v6 Smart FV and 26 propagation-specific topics not contained in IFA v6 FO.
Similar to IFA v6 Smart FV and IFA v6 FO, IFA v6 PPM sees a reduction in the number of P&Cs originating mainly from merging P&Cs and from deletions.
A new P&C is introduced and opens the P&C document, requiring producer awareness of the risks (not necessarily a documented risk assessment) and critical production steps for controlling the traceability, origin, and plant health of the propagation material.
Overall, the specific propagation P&Cs were updated and adjusted based on input from stakeholders, e.g., the IFA PPM certificate holders.
Combinable crops version 6
IFA v6 CC is now in general alignment with other product categories of the IFA v6 Smart standard and mostly with IFA v6 Smart FV. Topics such as environmental responsibility and workers’ health and safety have been brought in line, as well as other elements such as food safety, production processes, traceability, etc.
P&Cs specific to the postharvest handling and long-term storage of combinable crops have also been addressed in this new version.
We would like to make you aware of an amendment in “GLOBALG.A.P. general regulations – Rules for plants scope” regarding the audit timing of initial audits. For combinable crops, the initial CB audit may take place either during harvest or as close as possible to the harvest, even after it, but only if the product is still on the farm where there is storage on farm.
The respective section 3.1.1 a) of “GLOBALG.A.P. general regulations – Rules for plants scope” is adapted to:
“The initial CB audit shall cover harvesting activities of each product to be included for certification, as well as product handling, if included. Other field work can be audited at a different time where feasible, but this is not obligatory. For combinable crops, the audit may take place either during harvest or as close as possible to the harvest, even after it, but only if the product is still on the farm where there is storage on farm.”
Legacy IFA: Technical news (discontinued solutions)
As previously communicated, IFA v5.2 Livestock scope will not exist anymore after end of 2023.
The last possible date for audits/inspections against IFA v5.2 livestock scope is 31 December 2023.
CBs can take the certification decision and issue certificates to IFA v5.2 livestock scope during 2024 as long as the audits have been conducted until 31 December 2023, but the validity of those certificates cannot be longer than 31 December 2024.
For more information and the related section in full, please see the full TN 03 2023 newsletter
Latest news
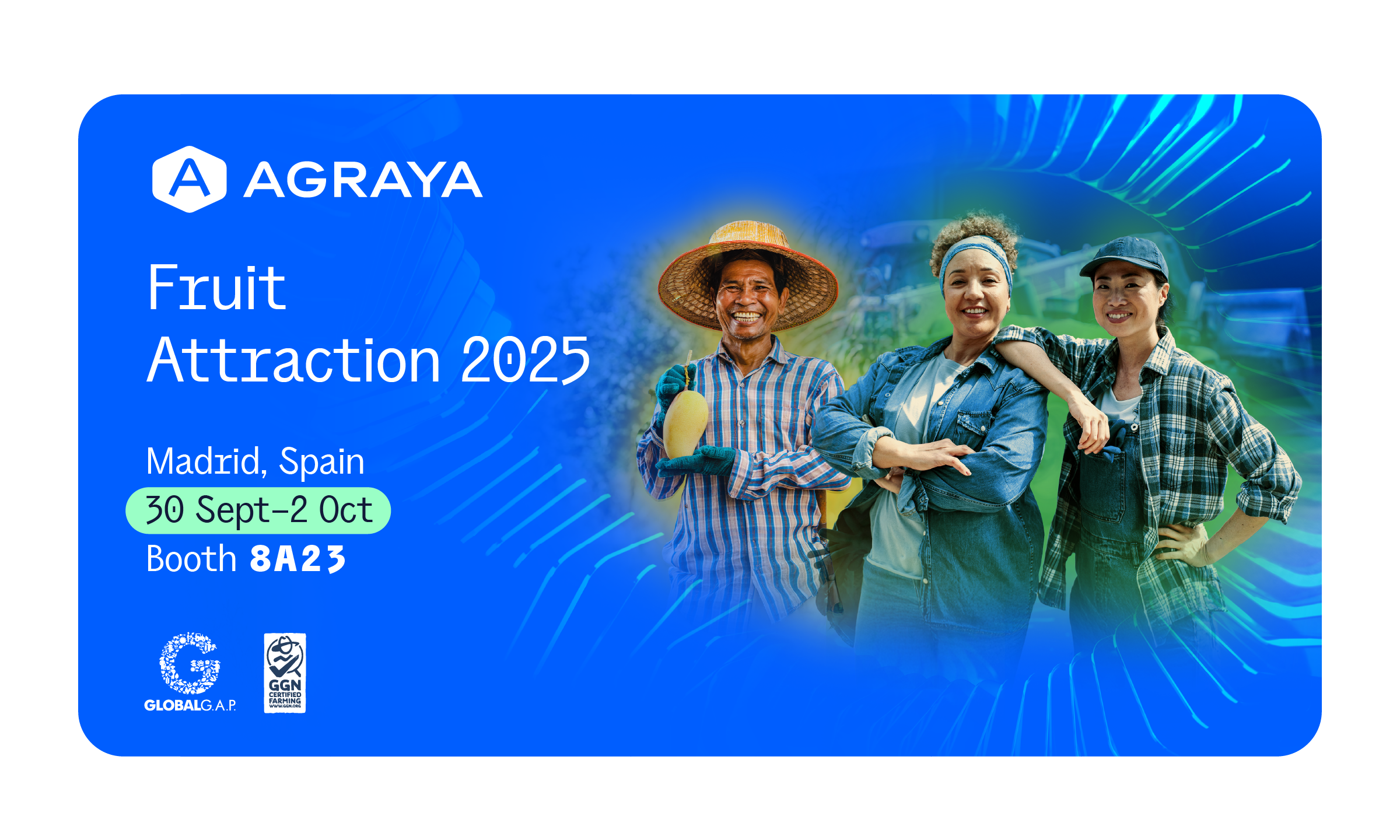
22 August 2025
Fruit Attraction 2025: AGRAYA unites GLOBALG.A.P. and the GGN label in Madrid
From 30 September to 2 October 2025, the Fruit Attraction trade fair in Madrid, Spain will be the stage for the next step in our journey.
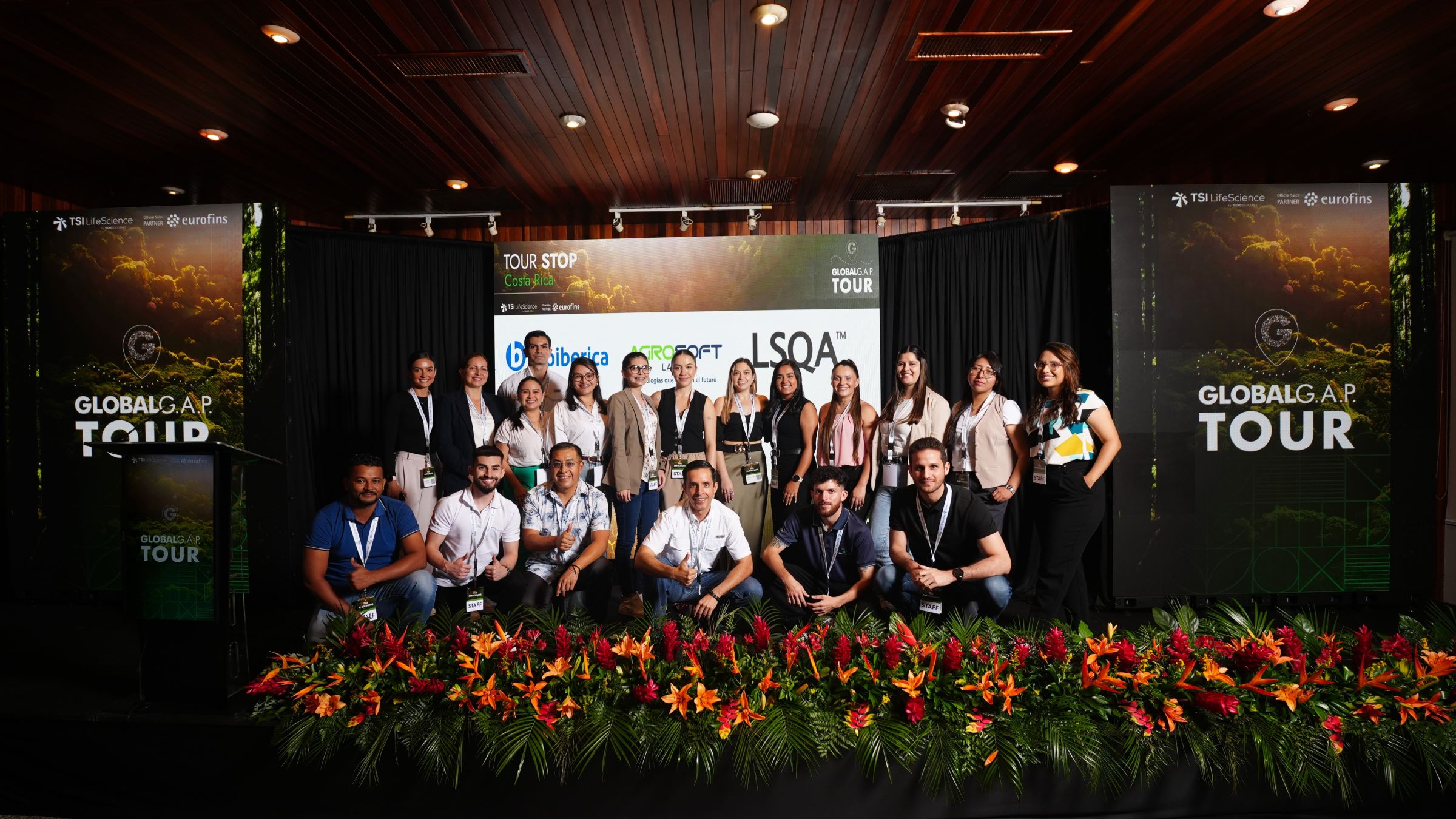
22 August 2025
Celebrating the first GLOBALG.A.P. TOUR stop in Costa Rica
From 31 July–1 August 2025, more than 130 participants attended the capacity-building event hosted in partnership with TSI Life Science-Eurofins.
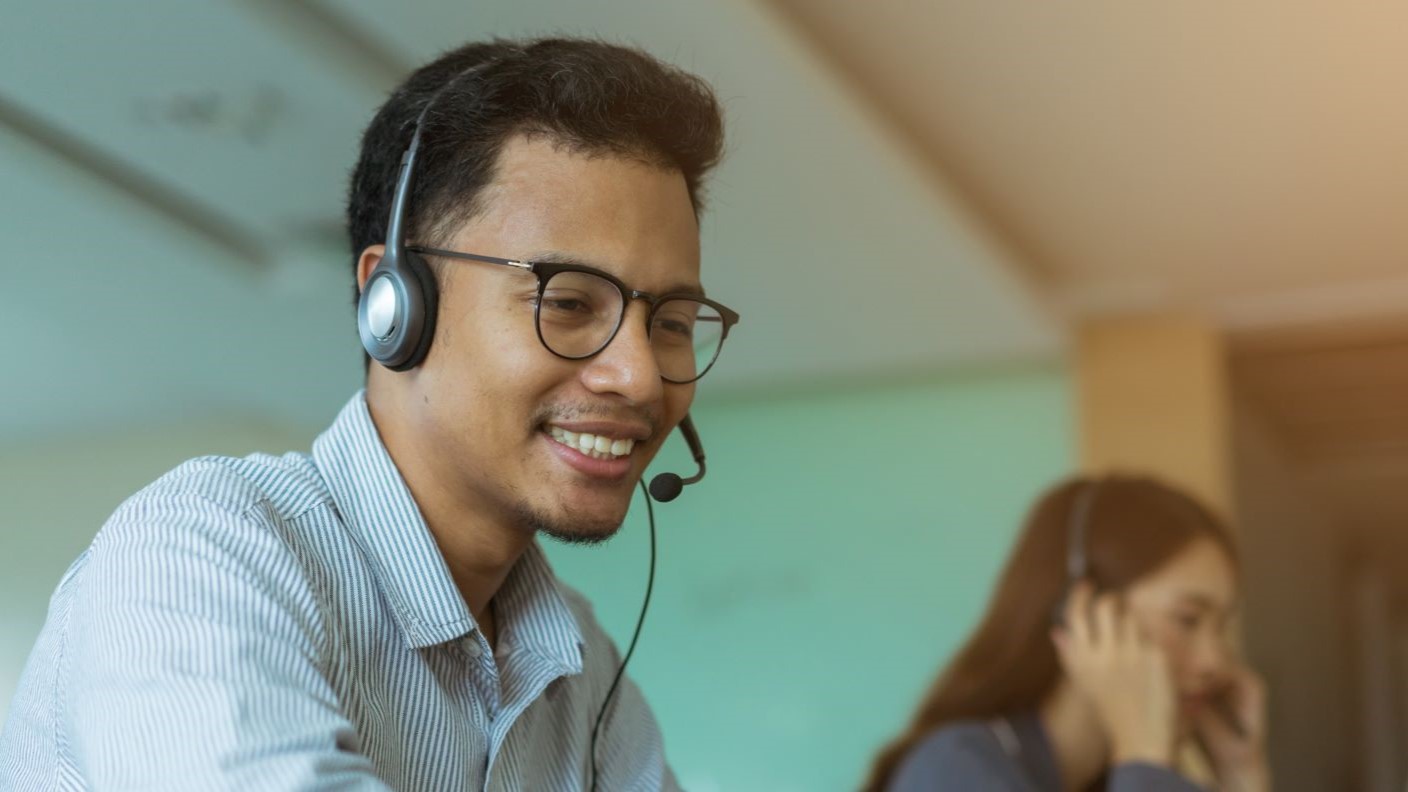
Contact us
For technical support on GLOBALG.A.P. solutions, please contact us at standard_support@globalgap.org.
For general questions, please contact us at customer_support@globalgap.org.